· Lawn Mower Maintenance · 14 min read
Lawn Mower Ignition Switch Problems
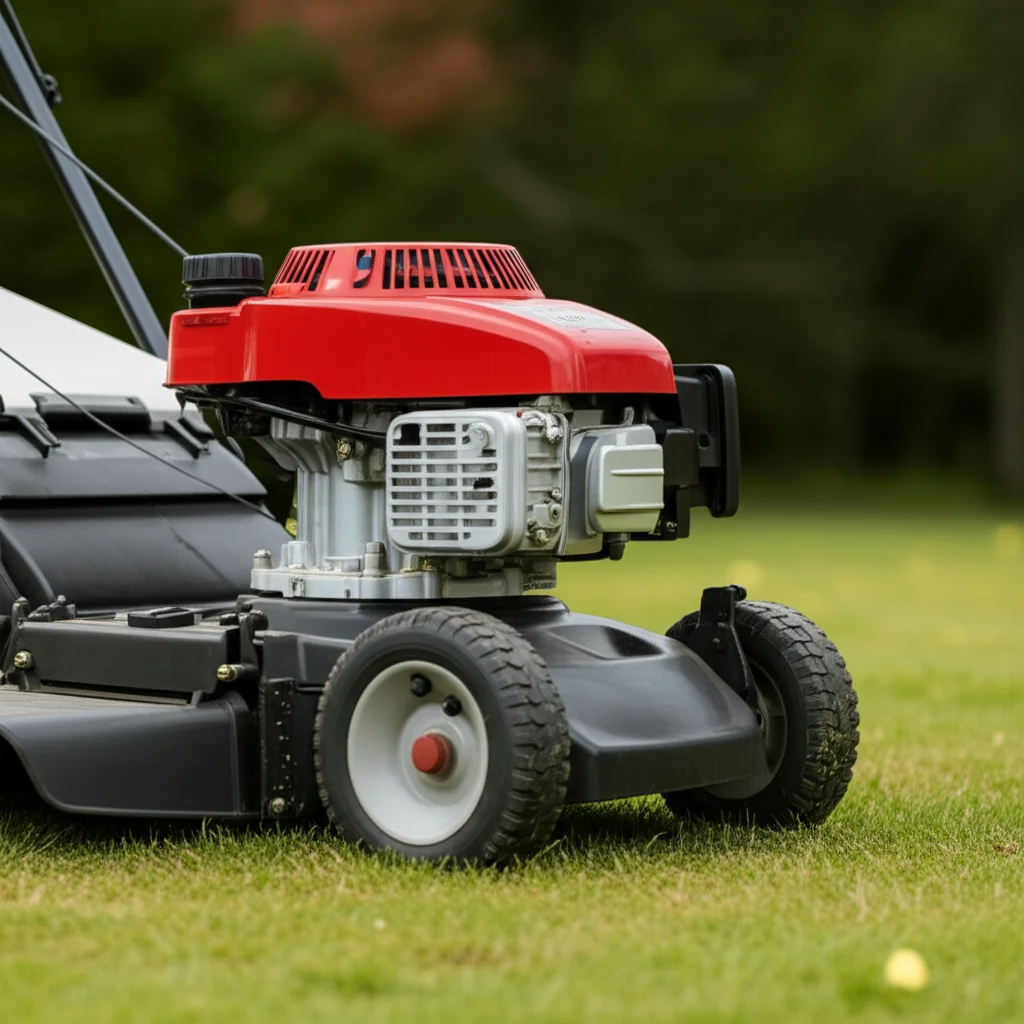
Lawn Mower Ignition Switch Problems: Complete Troubleshooting Guide
When you turn the key on your lawn mower and nothing happens, it’s often a frustrating experience that can ruin your lawn care plans.
Lawn mower ignition switch problems are among the most common issues homeowners face, yet they’re frequently misdiagnosed or overlooked entirely.
Understanding how to identify, troubleshoot, and fix these problems can save you time, money, and the headache of dealing with a non-functional mower when you need it most.
Key Takeaways
• Common symptoms include no response when turning the key, intermittent starting, and complete electrical failure
• Safety switches and wiring connections are often the real culprits behind ignition problems
• DIY diagnosis can be performed using basic multimeter testing and visual inspection
• Professional repair may be needed for complex electrical issues or when multiple components fail
• Prevention through regular maintenance and proper storage extends ignition switch lifespan
Quick Answer: When your lawn mower ignition switch fails, you’ll typically experience no engine response when turning the key, intermittent starting issues, or complete electrical system failure. Most problems stem from worn contacts, corroded connections, or faulty safety switches rather than the ignition switch itself.
Understanding Lawn Mower Ignition Systems
Modern lawn mowers rely on sophisticated ignition systems that work together to start your engine reliably. The ignition switch serves as the central command center, controlling power flow to various electrical components including the starter motor, ignition coil, and safety circuits.
The typical lawn mower ignition system consists of several key components: the ignition switch, starter solenoid, ignition coil, spark plug, and various safety switches. When you turn the key, the ignition switch sends power to the starter solenoid, which engages the starter motor. Simultaneously, it activates the ignition coil to generate the high-voltage spark needed for combustion.
Understanding this system helps you diagnose problems more effectively. Many homeowners assume the ignition switch is faulty when the real issue lies elsewhere in the electrical system. Safety switches, in particular, can prevent starting even when the ignition switch functions perfectly.
Most riding mowers and lawn tractors use either a 3-prong or 5-prong ignition switch configuration. The number of prongs determines how many circuits the switch controls, with 5-prong switches offering more functionality for accessories like lights and power take-off systems.
Common Symptoms of Bad Ignition Switch
Recognizing the early warning signs of ignition switch failure can help you address problems before they leave you stranded with an unresponsive mower. The most obvious symptom occurs when you turn the key and absolutely nothing happens – no clicking sounds, no electrical activity, and no engine response whatsoever.
Intermittent starting problems represent another telltale sign of ignition switch issues. Your mower might start perfectly one day, then refuse to respond the next, only to work again after several attempts. This inconsistent behavior often indicates worn internal contacts within the switch that make sporadic connections.
You might also notice that certain electrical components stop working while others continue to function normally. For example, your headlights might work fine, but the starter motor won’t engage, or vice versa. This selective failure pattern suggests specific circuits within the ignition switch have failed while others remain operational.
Some lawn mowers exhibit unusual electrical behavior, such as accessories staying powered when the key is in the off position, or the engine continuing to run after you turn off the ignition. These symptoms indicate internal switch contacts are sticking or have welded together from excessive current flow.
Listen for changes in the sounds your mower makes during startup attempts. A healthy ignition system produces consistent clicking from the starter solenoid when you turn the key. If this sound becomes weak, intermittent, or disappears entirely, the ignition switch may not be sending proper voltage to the starting circuit.
Diagnosing Ignition Switch Problems
Proper diagnosis requires a systematic approach that eliminates other potential causes before condemning the ignition switch. Start by checking the obvious culprits: ensure the battery has sufficient charge, verify all connections are clean and tight, and confirm that safety switches aren’t preventing operation.
Husqvarna safety switch problems can often mimic ignition switch failures, making proper diagnosis crucial. Most riding mowers have multiple safety switches that must be satisfied before the engine will start – seat switch, brake pedal switch, PTO switch, and sometimes a neutral safety switch.
Use a digital multimeter to test the ignition switch systematically. With the key in the off position, you should measure zero voltage at all output terminals. When turned to the run position, the switch should provide battery voltage to the ignition circuit. In the start position, both the run and start circuits should show proper voltage.
Testing individual circuits helps identify which part of the switch has failed. Remove the wiring harness from the ignition switch and test continuity between the input terminal and each output terminal as you move the key through different positions. A good switch will show continuity only to the appropriate terminals for each key position.
Don’t overlook the wiring harness itself during diagnosis. Corrosion, loose connections, or damaged wires can create symptoms identical to ignition switch failure. Wiggle the wiring harness while attempting to start the mower – if operation changes, you’ve likely found a connection problem rather than a switch failure.
Troubleshooting Craftsman Lawn Tractor Issues
Craftsman lawn tractors present unique challenges when diagnosing ignition problems due to their specific wiring configurations and safety switch arrangements. These machines often use proprietary ignition switch designs that require careful attention to wire color coding and terminal identification.
Craftsman riding mower steering problems sometimes coincide with electrical issues, particularly when both steering and ignition problems develop simultaneously. This combination often points to a common ground connection problem or main harness issue rather than individual component failures.
The most common Craftsman ignition switch problem involves the seat safety switch circuit. These mowers are particularly sensitive to seat switch operation, and even minor adjustments to seat position can prevent starting. Always ensure you’re properly seated and the seat safety switch is fully engaged before diagnosing ignition problems.
Craftsman models frequently experience starter solenoid issues that mimic ignition switch failure. The solenoid, usually located near the battery, may click weakly or not at all when the ignition switch activates. Testing voltage at the solenoid during key activation helps determine whether the problem lies with the ignition switch or the solenoid itself.
Many Craftsman tractors use a combination ignition switch and key switch assembly that can develop internal connection problems over time. These switches often have multiple small wires that can become loose or corroded, creating intermittent operation that’s difficult to diagnose without proper testing procedures.
How to Start Mower with Bad Ignition Switch
When faced with a completely failed ignition switch and an urgent need to cut grass, several temporary workarounds can get your mower running safely. These methods should only be used as emergency measures while you arrange for proper repair, as they bypass important safety systems.
The most straightforward bypass method involves connecting the starter solenoid directly to the battery. Locate the starter solenoid (usually a small cylindrical component near the battery) and identify the small terminal that normally receives power from the ignition switch. Using a jumper wire, connect this terminal directly to the positive battery terminal to engage the starter.
For mowers with separate ignition and starter circuits, you’ll need to provide power to the ignition coil as well. This typically involves connecting the ignition coil’s positive terminal to the battery through a manual switch or jumper wire. Remember that you’ll need to manually disconnect this power to stop the engine, as the normal ignition switch won’t function.
Always ensure all safety switches are properly engaged before attempting any bypass procedures. Even though you’re bypassing the ignition switch, safety switches like the seat switch and PTO switch should still be connected and functioning to prevent unsafe operation.
Consider using a temporary toggle switch to replace ignition switch functions during emergency repairs. Mount the switch in an accessible location and wire it to control both the ignition and starter circuits. This provides a more controlled and safer temporary solution than using jumper wires.
Never attempt to bypass safety switches or operate the mower without proper safety precautions in place. These systems exist to prevent serious injury, and defeating them creates significant hazards for both the operator and bystanders.
Professional vs DIY Repair Options
Deciding whether to repair ignition switch problems yourself or hire a professional depends on your technical skills, available tools, and the complexity of the specific problem. Simple ignition switch replacement often falls within the capabilities of most DIY enthusiasts, while complex electrical troubleshooting may require professional expertise.
DIY repair makes sense when the problem is clearly isolated to the ignition switch itself, you have basic electrical testing equipment, and replacement parts are readily available. Most ignition switches cost between $15-50, making replacement economical compared to professional service calls.
However, Husqvarna riding mower electrical problems and similar complex issues often require professional diagnosis to avoid costly mistakes. Professional technicians have specialized diagnostic equipment and experience with manufacturer-specific wiring configurations that can save time and prevent further damage.
Professional repair becomes necessary when multiple electrical components fail simultaneously, when wiring harness damage is extensive, or when safety switch integration is complex. These situations often indicate underlying problems that require systematic diagnosis and repair beyond typical DIY capabilities.
Consider the total cost of professional repair versus replacement when making your decision. If repair costs approach the price of a new mower, replacement might be the more economical choice, especially for older machines with multiple developing problems.
Time constraints also factor into the decision. Professional repair typically takes 1-3 days depending on parts availability, while DIY repair can often be completed in a few hours if you have the necessary parts and tools on hand.
Briggs & Stratton Specific Solutions
Briggs & Stratton powered mowers require specific diagnostic approaches due to their unique ignition system designs and wiring configurations. These engines often integrate the ignition system more closely with engine control systems, creating different failure patterns than other manufacturers.
Briggs and Stratton lawn mower surging can sometimes be traced to ignition switch problems, particularly when the surging occurs only during startup or immediately after starting. This symptom combination often indicates intermittent connections within the ignition circuit.
Briggs & Stratton ignition coils have specific testing procedures that differ from generic testing methods. These coils often have internal safety circuits that can cause confusing symptoms when partially failed. Always use Briggs & Stratton approved testing procedures and replacement parts to ensure proper operation.
The kill switch circuit on Briggs & Stratton engines requires special attention during ignition switch diagnosis. This circuit grounds the ignition coil to stop the engine, and problems here can cause both starting difficulties and engine shutdown issues. Test this circuit separately from the main ignition circuit to avoid misdiagnosis.
Many Briggs & Stratton powered mowers use integrated ignition modules that combine traditional ignition coil functions with electronic controls. These modules require different testing procedures and often need complete replacement rather than repair when they fail.
When replacing ignition components on Briggs & Stratton engines, always match part numbers exactly rather than using “universal” replacements. The specific timing and electrical characteristics of these components are critical for proper engine operation and using incorrect parts can cause performance problems or damage.
Prevention and Maintenance Tips
Regular maintenance significantly extends ignition switch life and prevents many common failure modes. Most ignition switch problems develop gradually due to environmental exposure, electrical stress, or mechanical wear that proper maintenance can minimize or prevent entirely.
Keep ignition switch connections clean and protected from moisture, which is the leading cause of ignition system corrosion. Apply dielectric grease to electrical connections and ensure all connectors fit tightly without gaps that allow water intrusion. Replace any connectors that show signs of corrosion or damage before they cause more extensive problems.
Inspect wiring harnesses regularly for signs of wear, particularly where wires pass through metal frames or near moving parts. Hydrostatic lawn mower transmission problems can sometimes create vibration that damages electrical connections over time, making regular inspection important for overall mower reliability.
Store your mower in a dry location when not in use, and consider disconnecting the battery during long-term storage to prevent discharge and corrosion. Battery discharge can create low-voltage conditions that stress ignition switch contacts and lead to premature failure.
Exercise the ignition switch periodically during storage by turning it through all positions several times. This prevents internal contacts from oxidizing and helps maintain proper electrical connections. However, avoid excessive cycling that might accelerate mechanical wear.
Replace ignition switches at the first sign of intermittent operation rather than waiting for complete failure. Early replacement prevents the frustration of unexpected breakdowns and often costs less than emergency repairs when you need the mower urgently.
Frequently Asked Questions
What are the symptoms of a bad ignition switch on a lawn mower? The most common symptoms include no response when turning the key, intermittent starting problems, electrical components that don’t work properly, and engines that won’t shut off when the key is turned to the off position. You might also hear weak clicking sounds from the starter solenoid or experience complete electrical system failure.
How do I know if it’s the starter or the ignition switch? Test the ignition switch by checking voltage at the starter solenoid when the key is turned to start. If you get proper voltage at the solenoid but the starter doesn’t engage, the starter or solenoid is likely faulty. If there’s no voltage at the solenoid, the ignition switch or its wiring is probably the problem.
When I turn the key on my lawn mower and nothing happens, what should I check first? Start with the basics: verify the battery is charged, check that all safety switches are properly engaged (seat, brake, PTO), and ensure all electrical connections are clean and tight. These simple issues cause the majority of “no start” conditions that homeowners attribute to ignition switch failure.
Can a bad ignition switch cause intermittent starting problems? Yes, worn internal contacts in the ignition switch can create intermittent connections that result in unpredictable starting behavior. The mower might start perfectly one day and refuse to respond the next, making this one of the most frustrating symptoms to diagnose and repair.
What’s the difference between a 3-prong and 5-prong ignition switch? A 3-prong switch typically controls basic ignition and starter circuits, while a 5-prong switch adds control for accessories like lights, power take-off, or other electrical systems. The additional circuits provide more functionality but also create more potential failure points.
How much does it cost to replace a lawn mower ignition switch? Ignition switches typically cost $15-50 for the part, with professional installation adding $75-150 in labor charges. DIY replacement can usually be completed in 1-2 hours with basic tools, making it an economical repair for most homeowners.
Can I bypass a bad ignition switch temporarily? While temporary bypasses are possible for emergency situations, they should only be used briefly and with extreme caution. Bypassing safety systems creates significant injury risks, and temporary repairs often cause additional electrical problems if left in place too long.
Final Words
Lawn mower ignition switch problems don’t have to leave you stranded with an overgrown yard. By understanding the symptoms, mastering basic diagnostic techniques, and knowing when to seek professional help, you can keep your mower running reliably throughout the mowing season. Remember that many apparent ignition switch failures actually stem from other electrical issues, making proper diagnosis essential before replacement.
Whether you’re dealing with a Craftsman M220 lawn mower that won’t start or complex electrical problems in your riding mower, the key to successful repair lies in systematic troubleshooting and attention to safety. Regular maintenance and prompt attention to early warning signs can prevent most ignition switch problems from developing into major repair issues.
Don’t let ignition switch problems keep you from maintaining your lawn properly. With the right knowledge and approach, these common issues become manageable maintenance tasks rather than overwhelming repair challenges. Take action at the first sign of problems, and you’ll save both time and money while keeping your mower running smoothly for years to come.