· Lawn & Garden Equipment · 23 min read
John Deere 2210 Problems
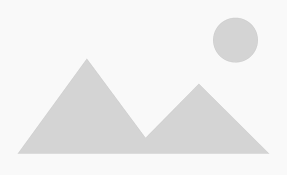
Deep Dive into John Deere 2210 Problems & Solutions
Is your John Deere 2210 giving you trouble? Many owners experience similar issues with this popular compact tractor. This article dives into the most common John Deere 2210 problems, offering insights into causes and potential solutions.
We’ll cover everything from transmission woes to engine difficulties, helping you keep your tractor running smoothly. Understanding these issues can save you time and money on repairs, and get you back to work faster.
Takeaway:
- Regular maintenance is key to preventing many John Deere 2210 problems.
- Hydrostatic transmission issues are a frequent concern, often requiring fluid checks or pump replacement.
- Engine problems can range from simple fixes like cleaning the fuel tank to more complex repairs.
A. Power Take-Off (PTO) System Failures
Problem: Catastrophic PTO failure, often occurring at low operational hours.
Description: Owners of the John Deere 2210 have frequently reported alarming symptoms related to the Power Take-Off (PTO) system. These include sudden, loud noises, often described as a “WHACK” or a distinct gear clashing sound, the PTO shaft becoming visibly off-center or off-axis, and hydraulic fluid leaking profusely from the PTO seal. In some documented cases, owners observed erratic engine idling just prior to a catastrophic PTO failure.
Cause:
- Tiller-Induced Stress: A disproportionately high number of catastrophic PTO failures, some occurring with remarkably low operational hours (as few as 30-116 hours), have been reported when using tillers, including John Deere’s own brand tillers.
Dealers have occasionally attributed these failures to the tiller PTO shaft being excessively long, creating an “axial load” that stresses the tractor’s PTO mechanism. However, many experienced owners, including those with extensive mechanical backgrounds, have challenged this explanation, suggesting a fundamental “gear failure” or an inherent design weakness within the 2210’s PTO system.
These owners often note that there was ample clearance for their tiller shafts, indicating that shaft length was not the root cause. This divergence in opinion points to a potential design limitation or a mismatch between the tractor’s perceived capability and its actual robustness when paired with common, heavy-duty implements.
- Slip Clutch Issues: The PTO’s slip clutch is engineered to protect the system from overload by allowing controlled slippage under excessive torque. However, if this clutch is not regularly engaged and lubricated, it can become stiff or rust.
A malfunctioning slip clutch fails to absorb shock loads effectively, transferring excessive strain directly to the PTO gears and shaft, which can lead to premature wear and failure.
- Incorrect PTO Shaft Length and Insufficient Lubrication: PTO shafts that are too long can bind when an implement is raised, leading to compression damage to the shaft itself, connecting components, or bearings.
Similarly, inadequate lubrication of the telescoping sections and shield bearings within the PTO shaft assembly can cause increased friction and accelerated wear, compromising the integrity of the system.
- Operational Habits: Improper operational habits, such as driving away or backing up the tractor without first disengaging the PTO, can also inflict significant and avoidable damage on the shaft and connected components over time.
Solution:
Regular PTO Shaft Inspection: It is advisable for owners to make a habit of visually inspecting the PTO shaft for any signs of misalignment, fluid leaks, or physical damage both before and after each use.
Slip Clutch Maintenance: Crucially, before each use, especially after periods of storage, operators should ensure their slip clutch is operational. This involves loosening its adjustment bolts, allowing it to slip, and then re-tightening it just enough to prevent slippage under normal working loads. This simple preventative step can avert significant and costly damage.
Verify PTO Shaft Length: Owners should confirm that their PTO shaft is the appropriate length for the specific implement being used. There should be sufficient play when the implement is fully raised to avoid binding or excessive compression. Shortening the shaft may be necessary if it is too long.
Consistent Lubrication: Lubricating the PTO telescoping tubing and shield bearings regularly, ideally every 8 hours of operation, is recommended to minimize friction and wear.
Safe Operation: Operators should always remember to disengage the PTO before moving the tractor, particularly when backing up, to prevent unnecessary strain and damage.
B. Hydrostatic Transmission & Hydraulic System Issues
Problem: Loss of drive power, unusual noises, and fluid leaks.
Description: Owners of the John Deere 2210 frequently report a range of symptoms related to the hydrostatic transmission and hydraulic system.
These include a noticeable loss of drive power, the tractor unexpectedly shutting off when shifted out of neutral, a distinct whining noise (especially pronounced when climbing hills or under heavy load), difficulty in shifting between forward and reverse, and an overall sluggishness in operation. Furthermore, visible fluid leaks (manifesting as puddles under the tractor or dampness around fittings or hoses) and system overheating are critical indicators of underlying hydraulic problems.
Cause:
Safety Switch Malfunctions: A very common cause for the tractor shutting off or failing to run when moved out of neutral is a faulty seat safety switch. These switches can become stuck, freeze in cold weather, or simply wear out over time, preventing the necessary electrical circuit from closing. The PTO safety switch can also trigger similar shutdown issues if it is activated or malfunctioning.
Low or Contaminated Hydraulic Fluid: The hydraulic system is integral to the hydrostatic transmission, operating at very high pressures, typically between 3000-4000 psi.
Insufficient fluid levels, contaminated fluid (due to dirt, debris, or water intrusion), or using the incorrect fluid type or viscosity can lead to reduced performance, overheating, and accelerated wear on critical internal components.
Clogged Filters: Clogged hydraulic filters severely restrict the flow of fluid, forcing the hydraulic pump and other components to work harder to maintain pressure. This results in decreased pressure, reduced flow rates, and can quickly lead to system overheating, which in turn degrades the fluid and components.
Worn Components (Pumps, Seals, Hoses): Internal leakage within the hydraulic pump due to worn seals or damaged components is a common cause of low pressure and reduced efficiency.
Hydraulic hoses are susceptible to cracks, swelling, or leaks around fittings due to age, constant flexing, and the high operating pressures. Over time, the hydrostatic transmission’s internal components or the hydraulic pump itself may simply wear out, necessitating a costly rebuild.
Air in the System (Cavitation): Air bubbles trapped within the hydraulic system, a condition known as cavitation, can cause sluggish operation, inconsistent power delivery, and a distinct whining noise. This is particularly common after prolonged storage or following hydraulic system service where air may have entered the lines.
Mechanical Linkage Issues: Sometimes, stiffness in the forward/reverse foot pedals or difficulty shifting gears can be attributed to external linkages that are rusted, obstructed by debris, or simply require lubrication, rather than an internal transmission fault.
Solution:
Safety Switch Check: Operators should thoroughly inspect the seat and PTO safety switches to ensure they function correctly, spring back to their original position, and are free from obstructions or freezing.
Fluid Management: Regularly checking hydraulic fluid levels and condition is paramount. It is essential to always use the manufacturer-recommended type and viscosity of fluid. Fluid should be replaced immediately if it appears contaminated or degraded.
Filter Maintenance: Adhering to the recommended replacement schedule for hydraulic filters (initially after 50 hours, then every 200 hours) and ensuring tank in-line strainers are thoroughly cleaned is crucial for maintaining proper flow and preventing contamination.
Purging Air: If the tractor exhibits sluggishness or a whining sound, especially after storage or recent service, operators should purge any trapped air from the hydraulic drive system by following the specific procedure outlined in the operator’s manual.
Leak Detection & Repair: Routine visual inspections of all hydraulic hoses, connections, and seals for any signs of leaks, dampness, or deterioration are recommended. Operators should also listen for unusual sounds like ticking, rumbles, or whining, which can indicate air leaks or internal issues.
Promptly addressing any leaks by replacing damaged lines, seals, or repacking cylinders is vital. A drive shaft lock rebuild kit (part numbers AM133973/AM132010) may be necessary for specific transmission issues related to ball bearings and springs.
- Linkage Lubrication: If foot pedals or levers feel stiff or sticky, operators can often resolve this by lubricating their external linkages with an appropriate product like WD-40.
The intrinsic link between the hydrostatic transmission and the hydraulic system, with the hydraulic pump often integrated directly into the transaxle, means that seemingly minor hydraulic issues can rapidly escalate into major transmission problems.
The high operating pressures inherent in these systems make even small leaks or contaminated fluid a significant concern, leading to reduced performance, overheating, and potential safety hazards.
This interconnectedness underscores that meticulous preventative maintenance of fluids, filters, and seals is not merely a good practice; it is a critical, proactive strategy to avoid costly, systemic failures and ensure the long-term reliability and safety of the John Deere 2210.
C. Engine Performance Problems (Yanmar Diesel)
Problem: Rough idling, stalling, reduced power, and unusual noises.
Description: Owners of the John Deere 2210 frequently report a range of engine performance issues, particularly with its Yanmar diesel engine. These symptoms include rough idling, sudden stalling (especially when coming out of neutral), difficulty starting, a noticeable reduction in power, the engine missing under load, and various unusual noises such as thumping, knocking, grinding, or squealing.
Additionally, changes in exhaust color, such as black, white, or blue smoke, can be tell-tale signs of underlying problems within the combustion process.
Cause:
Fuel System Issues: This is a very common and multifaceted area of concern for diesel engines. Problems can stem from stale or contaminated fuel (which may contain water, algae, or sediment), plugged fuel filters, air trapped in the fuel lines (often after running the tank dry or replacing filters), a clogged fuel tank vent (leading to a vacuum that starves the engine of fuel), and malfunctioning fuel injectors or fuel pumps. Poor-quality fuel is a significant contributor to deposits and premature wear within the entire fuel system.
Low Compression: Critical for diesel engine ignition, low compression can be caused by worn valve guides, cylinder wear, sticking piston rings, or a blown head gasket (often indicated by persistent bubbles in the radiator).
Yanmar-specific vulnerabilities include corroded valve seats, which can result from a faulty exhaust elbow design that allows water intrusion into the cylinders over time.
Air Intake Blockages: A restricted air supply forces the engine to work harder and can lead to poor combustion, overheating, or stalling. Common culprits include clogged air filters (both foam pre-cleaners and paper elements) or, less obviously, internal muffler baffles that have collapsed and blocked exhaust flow, impeding the engine’s ability to “breathe”.
Incorrect Oil Viscosity/Contamination: Using engine oil with the wrong viscosity or operating with fuel-diluted oil can lead to inadequate lubrication and accelerated engine wear. Prolonged use of dirty engine oil and neglected oil filters can cause severe internal issues like crank damage and abnormal oil pressure drops, as metal particles circulate and cause friction.
Overloading: Consistently operating the tractor under heavy loads, especially in hot ambient temperatures, can push the engine beyond its design limits, leading to overheating and premature wear on components.
Solution:
- Comprehensive Fuel System Checks: Operators should begin by inspecting the fuel tank for any signs of contamination. If contamination is suspected, draining the old fuel and refilling with fresh, clean diesel is recommended. Fuel filters should be replaced regularly (recommended every 400 hours or annually).
If the engine ran dry or a filter was recently changed, bleeding any air from the fuel lines is necessary. Testing fuel pump pressure and visually inspecting the fuel injector spray pattern for an even mist, rather than a stream or drips, can help diagnose fuel delivery issues.
Air Intake System Inspection: Cleaning the foam pre-cleaner element regularly is important. The paper air filter element should be replaced when dirty; it is crucial never to attempt to clean it by wiping or blowing air, as this can cause damage and compromise filtration. The muffler should also be checked for any internal blockages that might restrict exhaust flow.
Compression Test: Performing a diesel compression test is a key diagnostic step (a healthy Yanmar diesel engine can show close to 600 psi; readings below 400 psi typically indicate starting difficulties). If compression is low, removing valve covers to inspect for loose/broken rockers, worn valve guides, or signs of water intrusion is advisable.
Cooling System Verification: Operators should ensure coolant levels are correct, radiator fins are clean and unobstructed, and the cooling fan and water pump are functioning properly to maintain optimal engine temperature.
Oil Maintenance: Always using the correct engine oil viscosity for operating conditions is vital. Strictly adhering to recommended oil and filter change intervals is paramount for preventing the circulation of harmful metal particles and avoiding severe internal engine damage.
The detailed examples of Yanmar engine failures, ranging from crank damage due to dirty oil to fuel injection issues caused by contaminated fuel, clearly demonstrate that neglecting routine filtration and fluid maintenance is not merely a minor oversight but a direct pathway to catastrophic internal engine damage.
Furthermore, the specific vulnerability of corroded valve seats linked to a known faulty exhaust elbow design highlights a critical design characteristic unique to some Yanmar engines.
This transforms a seemingly simple exhaust component into a point of particular weakness that, if not proactively monitored or replaced, can lead to severe compression loss and ultimate engine failure. This emphasizes that consistent, high-quality filtration and addressing known design characteristics are absolutely paramount for the longevity and reliable operation of the Yanmar engine in the John Deere 2210.
D. Electrical System Glitches
Problem: Starting issues, battery drain, and erroneous warning lights.
Description: Electrical problems in the John Deere 2210 can manifest in various frustrating ways. The most common are starting issues, such as the tractor not cranking at all, producing only a clicking sound, or cranking very slowly and weakly.
Other symptoms include chronic battery drain, intermittent or erroneous warning lights on the dash, and even unexpected issues like a rough idle or incorrect sensor readings (e.g., extreme temperature readings) immediately after the battery has been disconnected and reconnected.
Cause:
Battery Issues: A low charge or a completely dead battery is the most frequent cause of starting difficulties. Corroded or loose battery terminals and cables can also prevent sufficient electrical current from reaching the starter motor and other components.
Blown Fuses: Faulty or blown fuses are common culprits that can interrupt the electrical supply to essential components like the fuel solenoid, ignition system, or the starter motor itself, preventing proper operation.
Faulty Voltage Regulator: A malfunctioning voltage regulator (part numbers M807915, 15531-64603 are noted as replacements for the 2210) can lead to improper battery charging, either overcharging (which damages the battery) or undercharging (which leaves it drained), causing a cascade of electrical symptoms.
Wiring Harness Damage: Exposed or poorly routed wiring harnesses are vulnerable to wear, abrasion, or even rodent damage, especially in areas near moving parts like wheels or linkages. This can lead to intermittent electrical faults that are notoriously difficult to diagnose due to their unpredictable nature.
Safety Switches: While often overlooked as purely electrical components, faulty safety switches (e.g., seat, PTO, brake) are wired in series within the electrical system and can prevent the engine from starting or continuing to run if they detect an unsafe condition or fail internally.
ECU/Computer Reset Anomalies: Modern tractors, like the 2210, incorporate onboard computers (ECUs). Disconnecting the battery can sometimes cause temporary glitches, such as a rough idle or incorrect sensor readings, which may necessitate a “hard reset” of the ECU to clear the transient errors.
Solution:
Battery Testing and Maintenance: Operators should begin by testing the battery voltage with a multimeter (it should read at least 12.6 volts when fully charged). Ensuring battery terminals and cables are clean and tightly connected is also crucial. The battery should be charged or replaced if it is low on charge or found to be faulty.
Fuse Inspection: Systematically checking all fuses and relays using a test light or multimeter is recommended to identify any blown components. Operators should always consult their owner’s manual for precise fuse box locations and diagrams.
Wiring Inspection and Repair: A visual inspection of all accessible wiring for signs of wear, corrosion, or loose connections is important, particularly around the starter, solenoid, and ignition switch. Addressing any poorly routed or damaged wiring harnesses by securing them and repairing bare wires can prevent future issues.
Safety Switch Verification: Operators should confirm that all safety switches (seat, brake, PTO) are functioning correctly and are not stuck or worn out, as these are critical for operation.
Voltage Regulator Check: If chronic battery charging issues persist despite a healthy battery, testing or replacing the voltage regulator should be considered.
ECU Hard Reset: If unusual symptoms like a rough idle or erroneous sensor readings appear immediately after battery work, a “hard reset” of the ECU (often by disconnecting it for a few minutes) may resolve the issue, clearing any transient electronic glitches.
Electrical problems in the John Deere 2210 are often particularly frustrating due to their intermittent nature and the wide range of seemingly unrelated symptoms they can produce.
The fact that a simple action like disconnecting the battery can lead to complex, temporary glitches highlights the sensitivity of the tractor’s integrated electronic systems.
E. Cooling System Overheating
Problem: Consistently high temperature readings and boiling coolant.
Description: The most direct and critical symptom of a cooling system problem in the John Deere 2210 is consistently high temperature readings on the tractor’s gauge or the illumination of overheating warning lights.
Other alarming signs include coolant boiling out of the overflow bottle, a noticeable reduction in engine performance, and unusual noises emanating from the engine bay, indicating stress on the system.
Cause:
Low Coolant Levels or Blockages: Insufficient coolant in the system or blockages within the radiator hoses can prevent proper heat transfer, leading to rapid temperature increases in the engine. Using an incorrect type of coolant can also compromise the system’s efficiency and lead to issues.
Clogged Radiator and Fins: Dirt, debris (such as straw, grass, or mud), or bent/crushed cooling fins can severely obstruct airflow through the radiator. This significantly reduces the radiator’s ability to dissipate heat, causing the engine to overheat.
Faulty Water Pump: A malfunctioning water pump will fail to circulate coolant effectively throughout the engine and radiator. This leads to localized hot spots and rapid overall overheating. Owners should watch for coolant leaks around the pump or unusual grinding/squealing noises, which can indicate a failing pump.
Cooling Fan Malfunction: The cooling fan is essential for pulling air through the radiator and maintaining optimal engine temperature. A broken fan blade or a faulty fan clutch will reduce this critical airflow.
A particularly notable issue for the John Deere 2210 is the transmission cooler fan, which is prone to breaking from debris ingestion. Its replacement is exceptionally difficult, often requiring the entire rear transaxle assembly to be removed or slid back, effectively meaning the “tractor has to be split” for access.
- Overloading: Consistently operating the tractor under heavy loads, especially during hot weather conditions, can push both the engine and hydraulic system beyond their designed cooling capacities, leading to overheating.
Solution:
Coolant Level and Condition: Operators should regularly check their coolant levels and ensure they are using the manufacturer-recommended type. If a blown head gasket is suspected, starting the engine with the radiator cap off and observing for consistent bubbles in the coolant can be a diagnostic indicator.
Radiator Cleaning: Keeping the radiator and its protective screens meticulously clean is vital. Using compressed air to blow out any accumulated dirt and debris from the fins is recommended. It is crucial never to use a pressure washer directly on the radiator, as this can easily damage the delicate fins.
Fan and Water Pump Inspection: Operators should visually inspect the cooling fan for any broken blades or signs of malfunction. The water pump should also be checked for leaks or unusual noises. It is important to be aware that if the transmission cooler fan is broken, this typically indicates a major and complex repair.
Belt Tension: Ensuring the fan belt is properly tensioned and free from damage is important, as it drives both the water pump and the fan, critical components for cooling.
Manage Load: Avoiding continuously overloading the tractor, particularly during peak summer heat, helps prevent unnecessary strain on the cooling system and extends component life.
Here is a summary of common John Deere 2210 problems:
Problem Area | Key Symptoms | Primary Causes | Immediate Action/Troubleshooting |
PTO System | Sudden noises, shaft misalignment, fluid leaks, erratic idle | Tiller-induced stress, slip clutch issues, incorrect shaft length, lubrication, operational habits | Inspect shaft, adjust/lubricate slip clutch, verify shaft length, ensure safe operation |
Hydrostatic Transmission & Hydraulics | Loss of power, whining, not staying in neutral, fluid leaks, overheating, shifting difficulty | Safety switch malfunctions, low/contaminated fluid, clogged filters, worn components (pumps, seals, hoses), air in system (cavitation), mechanical linkage issues | Check fluid, replace filters, purge air, inspect safety switches, fix leaks, lubricate linkages |
Engine Performance | Rough idle, stalling, hard starting, reduced power, smoke, unusual noises | Fuel system issues (stale/contaminated fuel, filters, air, vent, injectors/pumps), low compression (worn parts, blown gasket, Yanmar exhaust elbow), air intake blockages, incorrect oil/contamination, overloading | Check fuel quality/filters, inspect air cleaner/muffler, compression test, verify cooling system, maintain oil |
Electrical System | Starting issues (clicking, no response, slow cranking), battery drain, warning lights, erroneous sensor readings | Low battery, blown fuses, faulty voltage regulator, wiring damage, safety switches, ECU reset anomalies | Test battery, check fuses, inspect wiring, verify safety switches, check voltage regulator, perform ECU hard reset (if applicable) |
Cooling System | High temperature, boiling coolant, reduced performance, unusual noises | Low coolant, clogged radiator/fins, faulty water pump, cooling fan malfunction (transmission cooler fan), overloading | Check coolant, clean radiator, inspect fan/pump, verify belt tension, manage load |
IV. Preventative Maintenance: Keeping Your 2210 Running Strong
The single most effective strategy for minimizing problems, extending the operational life, and ensuring the reliable performance of the John Deere 2210 is diligent adherence to a consistent preventative maintenance schedule. Proactive care, rather than reactive repairs, can save owners substantial time, money, and frustration in the long run.
Key Maintenance Checkpoints:
Consult the Operator’s Manual: This cannot be stressed enough. The owner’s manual is the definitive guide for a specific 2210 model, providing precise maintenance intervals, recommended fluid types, and detailed procedures for various tasks.
Fluid and Filter Changes:
Engine Oil & Filter: Regular engine oil and filter changes are paramount for preventing internal wear, maintaining optimal compression, and ensuring the longevity of the Yanmar diesel engine.
Fuel Filter: The fuel filter should be replaced every 400 hours or annually, whichever occurs first. It is essential to always use clean, high-quality diesel fuel, and considering the addition of a winterizer/antigel product in cold climates can prevent fuel gelling.
Transmission/Hydraulic Oil & Filter: The hydraulic filter should be replaced initially after the first 50 hours of operation, and then every 200 hours thereafter. Crucially, maintaining proper fluid levels and ensuring the correct type and viscosity of hydraulic oil is used is vital, as this system powers both the transmission and implements.
Air Filter: The foam pre-cleaner element should be cleaned regularly. The paper air filter element should be replaced when dirty; it is critical never to attempt to clean it by wiping or blowing air, as this can cause damage and compromise its filtration capabilities.
Lubrication: Consistently greasing all specified lubrication points on the tractor is essential to prevent friction and premature wear on moving parts. Operators should be mindful not to mix incompatible grease formulations, as this can lead to lubrication breakdown and ineffective protection.
Visual Inspections: Developing a habit of routinely inspecting the tractor for any loose connections, signs of worn hoses, visible fluid leaks (especially hydraulic leaks), and accumulation of debris in the radiator fins or air intake screens can help catch problems early.
Safety Switch Checks: Periodically verifying the proper function of all safety switches, including the seat, PTO, and brake switches, ensures they are not stuck or worn, maintaining critical safety interlocks.
PTO Slip Clutch Maintenance: Ensuring the PTO slip clutch is free and operational before each use, especially after periods of storage, by performing the recommended adjustment, helps prevent binding and protects the PTO system.
Axle Bolts: For John Deere compact tractors, including the 2210 and other 2, 3, and 4 Series models, regularly checking and tightening the axle bolts is recommended, as they have been known to loosen over time.
Many of the most common and costly problems discussed for the John Deere 2210 are either directly preventable or their severity can be drastically reduced through diligent adherence to a consistent preventative maintenance schedule.
Here is a recommended maintenance schedule for the John Deere 2210:
Maintenance Task | Recommended Interval | Key Notes/Details |
Engine Oil & Filter Change | Per Operator’s Manual | Essential for engine health and compression. |
Fuel Filter Replacement | Every 400 hours or Annually | Use clean, quality diesel; consider winterizer in cold climates. |
Transmission/Hydraulic Oil Filter Replacement | Initial: 50 hours; Subsequent: Every 200 hours | Crucial for hydrostatic transmission and hydraulic system health. |
Grease All Points | Regularly (e.g., Every 8 hours of PTO use) | Prevents friction and premature wear; avoid mixing incompatible greases. |
Air Filter Cleaning/Replacement | Regularly (clean foam, replace paper) | Essential for optimal engine performance and longevity. |
Radiator & Screens Cleaning | Regularly (especially after dusty work) | Use compressed air; never pressure wash. |
PTO Slip Clutch Check/Adjustment | Before each use (especially after storage) | Ensures proper function and protects PTO from overload. |
Axle Bolts Check/Tighten | Periodically | Prevents loosening, a known issue on some compact models. |
Safety Switch Verification | Periodically | Ensures critical safety interlocks are functioning. |
General Visual Inspection | Before/After each use | Look for leaks, worn hoses, loose connections, debris. |
V. When to Call a Professional: Recognizing Limitations
While the spirit of DIY troubleshooting and repair is commendable and often effective for minor issues, there are certain problems with the John Deere 2210 that are best left to the expertise of certified professionals. Recognizing these limits is crucial for both the tractor’s longevity and the operator’s safety.
Identifying Issues Requiring Expert Intervention:
Catastrophic Failures: Any incident involving a sudden, severe breakdown, such as a cracked PTO shaft, internal transmission damage, or significant engine component failure, typically requires specialized diagnostic tools and repair techniques beyond the scope of a home mechanic.
Persistent Electrical Issues: If electrical problems persist after basic checks like battery testing, fuse inspection, and wiring visual checks have been performed, it is advisable to seek professional help. These issues can be complex and require advanced diagnostic equipment.
Complex Hydraulic System Diagnostics and Repairs: Issues requiring in-depth hydraulic system diagnosis, hydraulic pump replacement, internal cylinder repairs, or the specialized tools needed for crimping high-pressure lines fall into this category. Attempting these without proper knowledge can lead to further damage or safety hazards.
Internal Engine Problems: Any engine problem indicating significant internal wear, such as persistent low compression that is not resolved by fuel or air system checks, or the presence of unusual knocking or thumping noises, suggests internal component damage that requires professional assessment.
Repairs Requiring Specialized Disassembly: Certain repairs, such as the replacement of the transmission cooler fan, which necessitates “splitting” the tractor, require specialized equipment, extensive knowledge, and adherence to strict safety protocols that are typically beyond the capabilities of a home mechanic.
Importance of Official Manuals and Dealer Support:
Operators should always make their John Deere Operator’s Manual their first point of reference for specific troubleshooting steps, detailed maintenance schedules, and comprehensive wiring diagrams.
For complex or unresolved issues, contacting an authorized John Deere dealer or a trusted local mechanic is highly recommended.
These professionals have access to specialized diagnostic tools (such as John Deere’s ServiceADVISOR™ system), proprietary information, and factory-trained technicians who can accurately diagnose and repair complex problems, often more efficiently and safely.
Conclusion
Addressing John Deere 2210 problems promptly is key to maintaining its performance and longevity. From common issues like hydrostatic transmission failures and engine starting difficulties to fuel system clogs and hydraulic leaks, understanding these potential problems can save you time and money.
Remember that regular maintenance, including fluid checks, filter replacements, and thorough inspections, is the best way to prevent issues and keep your John Deere 2210 running reliably for years to come. Don’t hesitate to consult a qualified mechanic if you’re unsure about any repairs.