· Lawn & Garden Equipment · 21 min read
John Deere 2025r Problems
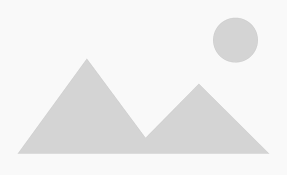
John Deere 2025r Problems: A Comprehensive Guide
Are you experiencing issues with your John Deere 2025r compact tractor? This popular model, known for its versatility, isn’t immune to problems. Many owners encounter similar challenges, and understanding these common issues can save you time and money.
This article will delve into the most frequently reported John Deere 2025r problems, offering insights into causes and potential solutions. We’ll cover everything from transmission difficulties to engine hiccups, helping you keep your tractor running smoothly.
Takeaway:
- Regular maintenance is crucial for preventing many 2025r problems.
- Hydrostatic transmission issues are a common concern, often related to fluid levels or filter clogging.
- Engine problems can stem from fuel delivery, cooling system issues, or sensor failures.
- Addressing issues promptly can prevent further damage and costly repairs.
The John Deere 2025r is a versatile compact tractor, but like any machine, it can experience issues. Here’s a quick answer: Common problems include hydrostatic transmission issues, engine starting difficulties, hydraulic leaks, and electrical glitches. Regular maintenance and prompt attention to warning signs are key to keeping your 2025r running reliably.
1. Critical Safety & Recall Alerts for the 2025R
Problem: Urgent Brake System Recall
Description: Approximately 147,900 compact utility tractors in the U.S. and an additional 16,800 units in Canada, encompassing the John Deere 2025R model (along with the 1023E and 1025R), are affected. The front bell crank within the brake linkage can fail, leading to a complete loss of braking capability and a severe “crash hazard.”
Four instances of brake linkage failure have been reported in the U.S., resulting in one hospitalization, two impact injuries, and minor damage to the affected tractors. The recall applies to tractors purchased from November 2017 through July 2024.
Cause:
Potential failure of the front bell crank within the brake linkage.
Solution:
Owners are strongly advised not to operate their recalled tractors until a free repair has been performed by an authorized John Deere dealer. If a consumer faces difficulties transporting the tractor to a dealership, the dealer is mandated to arrange for the repair to be conducted at the consumer’s residence.
Due to the extensive scale of this recall, John Deere is distributing repair parts in batches, prioritizing older model years (e.g., 2018-2019) first, which means that repairs for all affected units will take considerable time. Owners can verify their tractor’s recall status by entering its serial number on the official John Deere website.
Problem: Engine Shut-off & Operator Presence System Malfunctions
Description:
The 2025R incorporates an operator presence system designed to shut down the engine if the operator leaves the seat while the transmission, mid PTO, or rear PTO is engaged. While vital for preventing accidents, user reviews suggest this system can sometimes be overly sensitive or prone to issues.
One user reported an alarming incident where the engine stopped when the reverse pedal was pushed on a hill, causing the tractor to free-fall backward. Another observation noted that the neutral safety switch lacked an indicator light and was difficult to engage, frequently causing the tractor to shut off when the operator dismounted.
Cause:
Malfunctioning or overly sensitive operator presence system; a loose connection in the pedal linkage safety switch located under the seat.
Solution:
Troubleshooting efforts for similar issues have identified that tightening a loose connection in the pedal linkage safety switch under the seat can resolve intermittent PTO engagement.
John Deere faces the challenge of ensuring these systems are not only failsafe but also robust, reliable, and intuitive in their operation to prevent dangerous unexpected shutdowns or to discourage users from attempting workarounds that could compromise safety.
2. Mechanical & Hydraulic System Challenges
Problem: Persistent Hydraulic Leaks
Description:
Hydraulic fluid leaks represent a common complaint among 2025R owners, appearing in diverse locations and sometimes persisting even after multiple repair attempts. Symptoms include oil leaks observed under the tractor after mowing, specifically from the mid PTO seal, occasionally necessitating a full transmission replacement after repeated failed repairs.
Leaks have been reported originating from the transmission housing, steering fluid leaks, general oil leaks detected at the rear of the tractor, and issues at initial delivery where most backhoe attachment fittings had not been adequately tightened, leading to hydraulic fluid expelling everywhere upon the first use.
A “leaking differential” was also reported after a mere 5 hours of operation.
Cause:
Low hydraulic oil levels, damaged hoses, fittings, seals, gaskets, or O-rings. Early-onset problems and loose fittings upon delivery strongly point towards deficiencies in manufacturing or assembly line quality control.
Solution:
Initial troubleshooting steps involve checking fluid levels, visually inspecting for leaks, and tightening any loose connections. However, persistent leaks may indicate more severe internal wear or damaged components, necessitating professional assessment and part replacement.
For consumers, a thorough pre-delivery inspection by the dealer and a detailed initial inspection by the owner are critical, with immediate documentation of any detected issues to ensure appropriate warranty coverage.
Problem: Loader & 3-Point Hitch Performance Issues
Description:
Owners have observed issues with the performance and attachment of implements, particularly concerning the front-end loader and 3-point hitch.
Symptoms include the loader leaking down rapidly (e.g., dropping 41 inches in 6 minutes), difficulty in attaching the loader bucket, the backhoe requiring rebuilding after only an hour of use due to excessive leak down, and the backhoe lacking sufficient power to dig through small roots or the tractor struggling to back up a slight incline with a full bucket.
Raising the 3-point lever has caused the engine to labor and the independent mid hydraulics to rise autonomously.
Rear lift arms have been reported as not level, causing implements to tilt to one side, which necessitated adjustment of the spline. Hydraulic pressure relief has taken extended periods (hours to overnight) when switching between a loader and a grappler, complicating attachment changes.
Cause:
Low hydraulic fluid levels, air trapped within the hydraulic system, or clogged filters can all contribute to poor implement performance.
Leak-down issues frequently point to compromised seals, O-rings, or packing kits within the lift piston, or problems with the 3-point control valve. The iMatch Quick-Hitch system requires specific bushings for proper fit and function.
Solution:
Troubleshooting hydraulic issues should involve a comprehensive diagnostic process, beginning with fluid levels and cleanliness, then progressing to seals, hoses, and pump performance.
Addressing one hydraulic symptom often necessitates a holistic examination of the entire system. Owners should be aware that a seemingly minor leak could potentially escalate into broader performance issues across the hydraulic system.
Problem: Hydraulic Pump Noises & Efficiency
Description: Unusual noises emanating from the hydraulic system can serve as indicators of underlying problems that affect overall efficiency. A distinct whine from the hydraulic pump when the tractor is operating has been reported.
Cause: Whining or grinding noises can signal insufficient fluid levels, the presence of air in the system (a condition known as cavitation or aeration), internal wear within components, or inadequate lubrication. Low pressure can also be attributed to internal leakage or clogged filters.
Solution: Initial steps involve checking and topping off hydraulic fluid, bleeding any trapped air from the system, and inspecting or replacing filters. If the noise persists, a professional inspection of the pump’s internal components is advisable.
Owners should treat unusual hydraulic noises as critical early warning signs, as prompt investigation and resolution can prevent costly repairs and significantly extend the lifespan of the hydraulic system.
3. Engine & Fuel System Concerns
Problem: Starting Troubles
Description: Starting problems can be particularly frustrating, especially when the tractor is needed for immediate tasks. Symptoms include difficulty starting, often requiring multiple attempts, clicking sounds when the key is turned but without the engine cranking, the engine cranking slowly or weakly, and the engine catching briefly before dying.
A loud noise emanating from under the steering wheel when the key is turned to the on position has also been reported.
Cause: A weak or dead battery, a faulty starter motor, a worn ignition switch or a worn key itself, issues within the fuel system such as a clogged fuel filter, the presence of water in the fuel filters, or a malfunction in a safety switch.
Solution: Checking the battery charge and cleaning its terminals are fundamental first steps. Inspecting the starter motor for clicking sounds or a complete lack of response is also crucial. If the primary key shows signs of wear, trying a backup key may resolve the issue.
Replacing clogged fuel filters is a common fix for fuel delivery problems. The 2025R features an auto-bleeding fuel system, which means no special bleeding procedure is required if the tractor runs out of fuel. Troubleshooting starting problems necessitates a systematic approach that comprehensively examines both electrical and fuel pathways.
Problem: Engine Knock & Exhaust Smoke
Description: Some owners have observed specific engine noises and characteristics in the exhaust. Symptoms include a noticeable “engine knock between 1600-2000 RPMS” and excessive smoke during cold starts. Harsh diesel exhaust fumes when the front-end loader is in operation have also been noted.
Cause:
Faulty injectors, bearing failure (e.g., loose crankshaft bearings), insufficient oil pressure, or worn valve trains. While some smoke is normal for diesel engines during cold starts, persistent heavy smoke may indicate more serious fuel or combustion issues.
Solution:
For knocking sounds, it is advisable to check oil pressure, inspect bearings, and consider a professional diagnosis for potential issues with injectors or valve trains. Regular maintenance, including timely oil changes, is crucial for engine health.
Owners need to distinguish between typical diesel engine sounds and those that indicate a developing problem to seek professional assistance before minor issues escalate into major engine failures.
Problem: Overheating Issues
Description:
Overheating can occur, particularly during demanding tasks or in hot ambient conditions. Symptoms include the instrument panel displaying an “overheating” warning, leading to the tractor shutting down. Overheating has been observed when operating in hot weather.
Cause:
Clogged radiator fins and air intake screens, low coolant levels, or an incorrect coolant mixture.
Solution:
Regularly cleaning the radiator and its screens with compressed air is essential. Checking the coolant level and ensuring the correct mixture are also vital steps. It is important to ensure all protective screens are properly in place. This issue is largely preventable through diligent routine maintenance, especially when working in dusty or hot environments.
Problem: Power Perception & Fuel Gauge Design
Description:
User experiences sometimes touch upon perceived power limitations and specific design choices. Symptoms include a perceived lack of sufficient horsepower to effectively move wet snow, the engine bogging down on hills during mowing operations, and the relocation of the fuel gauge from the dashboard to the fuel tank, which some users found to make the machine “look and feel cheap” and described as a “nightmare.”
Cause:
The perception of the tractor being “underpowered” is subjective and often correlates with individual user expectations, as the 2025R is a compact tractor, not a commercial-grade heavy-duty machine. The fuel gauge relocation is a design choice that, while functional, negatively impacts the user experience and perceived quality.
Solution: Regarding power perception, ensuring that expectations align with the capabilities of a compact utility tractor is important. For the fuel gauge design, there is no direct fix, but owners typically adapt to the change.
Prospective buyers should test-drive equipment and thoroughly review specifications and user reviews to align personal expectations with the machine’s actual capabilities and design characteristics.
4. Electrical & PTO System Malfunctions
Problem: Battery & Charging System Reliability
Description:
Battery issues can lead to starting problems and broader electrical malfunctions. Symptoms include the battery dying after only two hours of use, battery failure necessitating a dealer repair, a “bad battery” reported after a mere 5 hours of operation, and the battery draining if the parking brake light is inadvertently left on.
Cause:
A weak or dead battery, a faulty alternator preventing the battery from charging effectively, or corroded or loose electrical connections. Reports of early battery failure suggest potential issues with the battery itself, the charging system, or parasitic electrical draws.
Solution: Checking the battery charge level and cleaning its terminals are important preventative measures. Testing the alternator’s functionality is also crucial. Regularly inspecting and cleaning all electrical connections can prevent many issues.
Some owners have reported that special tools may be required for battery removal and replacement, highlighting a design aspect that complicates basic maintenance.
Problem: PTO Engagement & Disengagement Failures
Description:
Problems with the Power Take-Off (PTO) can prevent attachments from operating correctly, significantly impacting the tractor’s versatility.
Symptoms include the PTO disengaging intermittently, then becoming a continuous issue, the PTO shifter kicking out of the “mid” position and into the “rear” position, and the PTO failing to engage or disengage as expected.
Cause:
A faulty PTO switch, a worn PTO clutch, various electrical issues (including problems with the wiring harness, ignition switch, seat safety switch, or relay control module), a low hydraulic oil level, excessive sideload or improper lubrication on the PTO clutch, physical damage or bearing failure within the clutch assembly, or a loose safety switch located under the seat pedal linkage.
Solution:
Testing the PTO switch for continuity is a key diagnostic step. Checking the under-seat safety switch and pedal linkage for proper contact is also essential. Inspecting wiring and fuses for damage or looseness is advised.
Verifying the hydraulic oil level and topping it off if low can resolve some issues. Inspecting the PTO clutch for wear or misalignment and ensuring proper lubrication are also important. Troubleshooting PTO problems requires a systematic diagnostic approach, extending beyond the obvious switch to meticulously check all interconnected components.
Problem: General Electrical Glitches
Description:
Beyond starting and PTO issues, general electrical problems can manifest in various ways, affecting different tractor functions. Symptoms include malfunctioning lights or gauges, intermittent power loss, issues with the climate control blower switch, a “flaky” and unprotected PTO switch located underneath the tractor, and a poorly positioned light switch that can lead to battery drain if inadvertently left on.
Cause:
Corroded or loose electrical connections, blown fuses, or a faulty alternator. The complaints regarding the PTO switch being “flaky” and “unprotected enough,” as well as the parking brake handle being positioned in a way that causes accidental engagement and battery drain, point to specific design vulnerabilities.
Solution:
Inspecting all wiring connections for signs of corrosion or looseness is crucial. Checking the fuse box for any blown fuses and replacing them as necessary can resolve many issues. Testing the alternator is important if battery charging problems persist. Owners should be particularly vigilant about inspecting vulnerable areas and consider aftermarket protective solutions if available.
5. Design Quirks & Quality Control Observations
Problem: Loose Fasteners & Structural Rattles
Description:
Reports indicate recurring issues with assembly quality and persistent, bothersome noises. Symptoms include bolts falling off the tractor and being found in the driveway, the tractor being delivered with loose nuts and bolts and even some missing pins, one front wheel detaching due to all lug bolts coming out after two years of ownership, and reports of the “tractor falling apart” after a few months.
An annoying rattle emanating from a slotted piece of metal near the fuel pump and a heat shield rattle (which in some cases led to the shield breaking) have also been reported.
Cause:
Systemic issues within the assembly or pre-delivery inspection process, rather than typical wear and tear.
Solution:
Regular inspection and tightening of all bolts and fasteners are essential preventative measures. Addressing rattles may involve bending components out of the way or seeking dealer repair.
This highlights the importance of dealerships conducting thorough pre-delivery inspections and ensuring all critical fasteners are securely tightened before the tractor is handed over to the customer.
Problem: Mower Deck & Propeller Shaft Vulnerabilities
Description:
Specific components, particularly those related to the mower deck and drivetrain, have demonstrated vulnerabilities that impact performance and durability.
Symptoms include the mower deck wheel shredding after only 2 hours of use, the mower deck brace coming apart, causing the deck to bang on supports after 7 hours, and grass and weeds wrapping around the propeller shaft, leading to the snapping off of the splined stub at the front of the transmission due to the absence of a protective guard.
The drive-on/off mower system has been reported as not functioning as advertised, occasionally catching the bucket stand, and difficulty experienced in attaching and detaching the mower deck, particularly for older individuals.
Cause:
Clear design flaws, such as the lack of a protective guard for the propeller shaft, rather than manufacturing defects.
Solution:
For the propeller shaft issue, a major warranty repair was necessary, but critically, no guard was added to prevent recurrence. Regular inspection of mower deck components is recommended. This indicates a lack of proactive design improvement by the manufacturer, suggesting a gap in John Deere’s product development cycle where known field issues are not being fully addressed with design revisions.
Problem: Operator Comfort & Control Placement
Description:
Ergonomics and the accessibility of controls have been points of contention for some users, affecting overall comfort and ease of operation. Symptoms include the parking brake handle being inconveniently positioned, frequently struck by the operator’s right foot, causing the light to turn on and drain the battery if unnoticed.
Users have reported a “stiff ride” and the observation that older models were more comfortable, with the current model sitting too high and feeling unstable on hills. Insufficient legroom for taller operators, with the seat not sliding back far enough, has been noted.
The absence of separate right and left brakes for tight turns and the differential lock pedal being a small rod that protrudes only about an inch, making it difficult to engage, are also concerns. Questions have been raised about the quality of the cab insulation, the interior cab light not being bright enough, and the exhaust pipe being positioned to blow fumes onto the tractor body.
Cause:
Inherent design trade-offs where some features appear to have regressed or are poorly executed, negatively impacting the daily user experience. The perceived instability on hills, despite the increased weight, points to a potential imbalance in stability design, possibly influenced by tire height.
Solution:
These issues, though not always leading to critical mechanical failures, significantly affect user satisfaction and productivity. They highlight the importance of holistic ergonomic design and extensive field testing with diverse user groups.
For prospective buyers, this reinforces the need to physically sit in and, ideally, operate the tractor to assess personal comfort and control accessibility before making a purchase.
Proactive Maintenance & Troubleshooting Guide
Regular maintenance is the cornerstone of tractor longevity and performance, helping to prevent many common issues and ensuring that the John Deere 2025R remains a reliable workhorse.
Essential Daily & Weekly Checks
Consistent routine checks can help detect problems early, preventing them from escalating into more significant issues.
- Daily Maintenance:
- Inspect for any visible damage, fluid leaks, or signs of wear on the machine.
- Check essential fluid levels, including engine oil, coolant, and hydraulic oil.
- Test all lights, dashboard gauges, and alarms to ensure full functionality.
- Clean air intake screens to prevent blockages that can restrict airflow.
- Apply grease to pivot points and other moving components to reduce friction and wear.
- Verify that tires are in good condition and properly inflated.
- Weekly Maintenance:
- Perform all daily maintenance tasks.
- Inspect and clean air filters; replace if necessary.
- Verify proper tension on all belts.
- Check the battery’s condition and clean its terminals to ensure good electrical contact.
- Inspect hydraulic hoses and fittings closely for any signs of wear or leaks.
- Test the parking brake and all other safety mechanisms to confirm they are fully functional.
Many reported issues, such as engine overheating or certain hydraulic problems, can be directly linked to neglected daily or weekly maintenance tasks like cleaning air filters or checking fluid levels.
These simple, quick checks, though often overlooked, are specifically designed to prevent minor issues from escalating into major, costly failures.
Scheduled Service Intervals (100, 250, 500 Hours)
Adhering to manufacturer-recommended service intervals is vital for the long-term health and performance of the tractor.
- 100-Hour Interval: Replace engine oil and the oil filter. Inspect and clean radiator fins. Test the alternator and starter motor. Check and tighten bolts on critical components. Lubricate all specified grease points. Inspect the steering and braking systems for proper operation.
- 250-Hour Interval: Perform all 100-hour maintenance tasks. Replace fuel filters and clean the fuel tank cap vent. Check and adjust valve clearance if applicable to the model. Inspect and replace hydraulic oil filters. Test hydraulic system pressure. Inspect wheel bearings for wear and damage.
- 500-Hour Interval: Perform all 250-hour maintenance tasks. Replace transmission oil and filter. Flush and replace coolant according to manufacturer guidelines. Inspect final drive oil levels and replace if necessary. Check for structural wear or cracks on key components. Test the entire electrical system, including wiring, connections, and lights.
Issues like engine knocking from low oil pressure or worn bearings, or persistent hydraulic problems stemming from contaminated fluid, are often the cumulative result of neglecting scheduled maintenance intervals. Scheduled maintenance is an investment in the tractor’s longevity and reliability, not merely an expense.
DIY Troubleshooting Tips
Many common issues can be diagnosed and, in some cases, resolved by owners themselves, reducing the need for immediate professional intervention.
- General Troubleshooting:
- Consistently check fluid levels (engine oil, coolant, hydraulic oil, transmission fluid).
- Inspect and clean all filters (air, fuel, transmission, hydraulic).
- Examine electrical connections for any signs of corrosion or looseness.
- Test switches (such as the PTO switch and seat safety switch) for proper continuity.
- Listen attentively for any unusual noises coming from the tractor.
- Specific Problem Solving:
- For PTO issues, specifically check the hydraulic oil level, the seat switch, and the pedal linkage safety switch.
- If experiencing starting difficulties, try using a backup key, as the primary key might be worn.
- For hydraulic leaks, look for visible fluid and tighten any loose hoses or fittings.
Providing clear, step-by-step troubleshooting guides empowers owners, reduces unnecessary visits to dealerships for simple fixes, and fosters a sense of self-reliance.
The Indispensable Operator’s Manual
The operator’s manual is the definitive resource for specific information regarding a particular tractor model.
- Importance: The manual contains critical maintenance guidelines, safety instructions, and troubleshooting information tailored specifically for the 2025R. It details proper operation and essential safety procedures.
- Available Resources: John Deere offers quick reference guides and the TractorPlus™ App, which provides access to manuals, allows for ordering parts, and facilitates searching diagnostic trouble codes (DTCs).
Despite the wealth of accurate information available in operator’s manuals and digital resources like the TractorPlus App, many users still turn to online forums or dealerships for initial troubleshooting.
Promoting these resources more aggressively and highlighting their practical utility can significantly improve owner self-sufficiency and reduce reliance on anecdotal or potentially incorrect advice.
Frequently Asked Questions (FAQ):
What is the major recall for the John Deere 2025R?
A: The John Deere 2025R is part of a recall affecting approximately 147,900 compact utility tractors (including 1023E and 1025R models) due to a potential failure in the front bell crank of the brake linkage. This can lead to a loss of braking and a crash hazard. Owners are advised not to operate the tractor until a free repair is performed by an authorized John Deere dealer.
Why is the John Deere 2025R’s PTO not engaging?
A: PTO engagement issues can stem from several causes, including a faulty PTO switch, a worn PTO clutch, or electrical problems with the wiring harness, ignition switch, or seat safety switch. A low hydraulic oil level can also prevent the PTO from engaging. Troubleshooting involves checking the PTO switch continuity, inspecting safety switches, and verifying hydraulic fluid levels.
Are hydraulic leaks common on the 2025R?
A: Yes, several owners have reported hydraulic leaks on their John Deere 2025R tractors, sometimes very early in ownership. Common leak points include the transmission housing, mid PTO seal, steering system, and backhoe attachment fittings. These leaks can be due to loose connections, worn seals, or damaged components, often requiring professional repair.
How does the 2025R compare to the 1025R in terms of common problems?
A: The 2025R and 1025R share many similarities, including the same hydrostatic transmission and PTO horsepower. While the 2025R is heavier and has a larger wheelbase and slightly higher lift capacity, some users perceive its power increase as minimal. Both models are subject to the same brake recall. Specific reported issues like hydraulic leaks and electrical glitches appear across the compact utility tractor range, though individual experiences vary.
What are the key maintenance tips for a John Deere 2025R?
A: Key maintenance tips include daily checks for leaks and fluid levels, weekly cleaning of air filters and battery terminals, and scheduled service at 100, 250, and 500 hours. These intervals involve changing engine oil and filters, fuel filters, hydraulic oil filters, and transmission oil. Always consult the operator’s manual for specific guidelines.
Is engine knocking normal for the 2025R?
A: While some diesel engine sounds are normal, persistent or specific engine knocking, especially between certain RPMs (e.g., 1600-2000 RPMS), is not. Engine knocking can indicate serious issues like faulty injectors, worn bearings, or low oil pressure. If unusual knocking is heard, it is advisable to investigate promptly or consult a professional.
Final Words: Maximizing Your 2025R’s Performance
The John Deere 2025R is a capable and versatile compact utility tractor, representing a valuable asset for many property owners. While no machine is entirely problem-free, understanding the common issues and proactive maintenance steps can significantly enhance the ownership experience. Addressing recalls promptly, staying vigilant for leaks, and performing regular checks on electrical and hydraulic systems will ensure the 2025R remains reliable.
The importance of the operator’s manual and the support of a local John Deere dealer should not be underestimated.
By combining informed ownership with consistent care, the tractor’s performance can be maximized for years to come. For any persistent issues or complex repairs, always consult an authorized John Deere service professional.