· Lawn Mower Maintenance · 10 min read
Zero Turn Mower Bogs Down When Cutting Grass
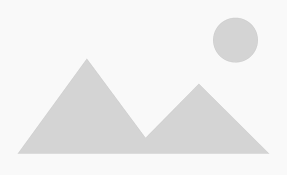
Zero Turn Mower Bogs Down When Cutting Grass: Expert Solutions
Is your zero turn mower losing power and bogging down when cutting grass, leaving you frustrated with uneven cuts and potential engine damage?
This comprehensive guide reveals the most common causes behind this issue and provides proven solutions to restore your mower’s peak performance, ensuring smooth operation across all grass conditions.
Key Takeaways
• Air filter blockage is the leading cause of power loss during cutting operations
• Dull or damaged blades create excessive engine load, causing bogging issues
• Carburetor problems restrict proper fuel-air mixture during high-demand cutting
• Deck height settings significantly impact engine performance in thick grass
• Regular maintenance prevents 80% of bogging problems before they occur
Quick Answer: Zero turn mowers typically bog down when cutting grass due to clogged air filters, dull blades, carburetor issues, or improper deck height settings. Most problems stem from inadequate maintenance or attempting to cut grass that’s too thick or wet for current mower conditions.
Understanding Why Zero Turn Mowers Bog Down
When your zero turn mower bogs down during cutting operations, the engine struggles to maintain proper RPMs under load. This phenomenon occurs when the power demand from cutting blades exceeds what the engine can efficiently deliver. Unlike starting issues that prevent operation entirely, bogging typically manifests as power loss specifically when blades engage with grass.
The cutting deck creates significant rotational resistance, especially in thick or wet conditions. Your mower’s engine must work harder to maintain blade speed while simultaneously powering the hydraulic drive system. When any component in this power delivery chain becomes compromised, bogging becomes inevitable.
Understanding this relationship helps identify why some mowers perform well on flat, thin grass but struggle in demanding conditions. The engine’s ability to maintain consistent power output directly correlates with proper maintenance and appropriate operating techniques.
Primary Causes of Zero Turn Mower Bogging
Air Filter Restrictions
Clogged air filters represent the most frequent culprit behind bogging issues. Your engine requires a precise air-to-fuel ratio for optimal combustion. When air filters become saturated with grass clippings, dust, or debris, airflow restrictions force the engine to run rich, reducing available power significantly.
Foam pre-filters often become completely blocked after extended use in dusty conditions. Paper air filters lose efficiency gradually but can reach critical restriction levels without obvious visual indicators. Regular inspection reveals whether your air filtration system allows adequate airflow for high-demand cutting operations.
Blade Condition Problems
Dull, damaged, or improperly installed blades create excessive drag on the cutting deck. Sharp blades slice through grass efficiently, while dull blades tear and push grass, requiring substantially more engine power. This increased load forces the engine to work beyond its optimal operating range.
Blade imbalance from damage or uneven wear creates additional problems. Vibrating blades waste energy and stress engine components unnecessarily. Multiple blade systems compound these issues when blades aren’t properly synchronized or maintained uniformly.
Carburetor and Fuel System Issues
Carburetor problems frequently cause intermittent bogging, especially during transition from idle to full-load cutting. Dirty carburetor jets restrict fuel delivery precisely when engines need maximum fuel flow. Ethanol-blended fuels exacerbate these problems by attracting moisture and creating deposits in carburetor passages.
Fuel delivery issues extend beyond carburetor problems. Clogged fuel filters, contaminated fuel, or failing fuel pumps prevent adequate fuel supply during high-demand operations. These problems often appear gradually, making diagnosis more challenging than sudden mechanical failures.
Engine-Related Bogging Factors
Spark Plug Performance
Worn or fouled spark plugs cannot provide consistent ignition under load. While engines may start and idle normally with marginal spark plugs, the increased compression and fuel mixture during cutting operations demands optimal ignition performance. Carbon buildup or incorrect gap settings compromise combustion efficiency precisely when power demands peak.
Compression Issues
Low engine compression reduces power output significantly during high-load operations. Worn piston rings, damaged valves, or head gasket problems allow combustion pressure to escape, preventing efficient power generation. These issues often develop gradually, making bogging problems progressively worse over time.
Compression testing reveals engine condition accurately. Engines with compression below manufacturer specifications struggle with demanding cutting conditions even when other systems function properly. Early detection prevents complete engine failure and costly repairs.
Cooling System Problems
Overheating engines automatically reduce power output to prevent damage. Blocked cooling fins, damaged cooling fans, or insufficient airflow create thermal conditions that trigger protective engine responses. Grass clippings frequently accumulate around engine cooling systems, gradually reducing heat dissipation efficiency.
Regular cleaning of cooling systems prevents thermal-related bogging. Engine compartments require thorough cleaning after each use in dusty or debris-heavy conditions. Proper airflow maintains optimal operating temperatures during extended cutting sessions.
Cutting Deck and Blade Issues
Deck Height Adjustments
Incorrect deck height settings force engines to work unnecessarily hard in thick grass conditions. Cutting too low in dense grass creates excessive load, while cutting too high may require multiple passes, increasing overall engine stress. Proper lawn mower cutting techniques ensure optimal performance across varying grass conditions.
Professional landscapers recommend following the “one-third rule” – never removing more than one-third of grass blade length in a single cutting session. This practice reduces engine load while promoting healthier grass growth and easier subsequent maintenance.
Blade Sharpening and Replacement
Sharp blades reduce cutting resistance dramatically compared to dull alternatives. Professional blade sharpening maintains proper cutting angles and edge geometry essential for efficient grass cutting. Attempting to sharpen severely damaged blades often proves less cost-effective than replacement.
Blade replacement schedules vary based on usage conditions and grass types. Commercial operators typically replace blades every 25-50 operating hours, while residential users may extend intervals to 50-100 hours. Regular inspection reveals when sharpening becomes insufficient for maintaining cutting efficiency.
Mulching Deck Considerations
Mulching decks create additional load compared to standard side-discharge configurations. The enclosed cutting chamber requires extra power to circulate clippings for proper mulching action. Attempting to mulch excessively thick or wet grass compounds these power demands significantly.
Converting between mulching and standard discharge configurations helps manage engine load during challenging cutting conditions. Many zero turn mowers allow quick deck configuration changes to match cutting demands with available engine power.
Fuel System Troubleshooting
Carburetor Cleaning and Adjustment
Systematic carburetor cleaning addresses most fuel-related bogging issues. Complete disassembly allows thorough cleaning of all jets, passages, and chambers. Professional carburetor troubleshooting techniques ensure proper fuel delivery across all operating conditions.
Carburetor adjustments require precision and proper tools. Main jet settings, needle valve positions, and idle mixture screws all affect performance under load. Documentation of original settings prevents over-adjustment and facilitates proper restoration if adjustments prove unsuccessful.
Fuel Quality and Storage
Fresh, high-quality fuel prevents many carburetor and fuel system problems. Ethanol-blended fuels attract moisture and create deposits that clog carburetor passages. Fuel stabilizers help maintain fuel quality during storage but cannot reverse contamination in degraded fuel.
Fuel storage practices significantly impact mower performance. Storing equipment with fresh fuel and appropriate stabilizers prevents seasonal starting and performance problems. Complete fuel system drainage before long-term storage eliminates contamination risks entirely.
Maintenance Solutions and Prevention
Regular Service Schedules
Preventive maintenance schedules eliminate most bogging problems before they develop. Air filter replacement, blade sharpening, and carburetor cleaning performed according to manufacturer recommendations maintain optimal performance throughout the equipment lifecycle.
Professional service intervals typically include:
- Air filter inspection every 25 hours
- Blade sharpening every 50 hours
- Carburetor cleaning annually
- Spark plug replacement every 100 hours
- Comprehensive engine service every 200 hours
Seasonal Preparation
Proper seasonal preparation prevents many performance issues. Pre-season service includes fuel system cleaning, air filter replacement, and blade inspection. Comprehensive zero turn troubleshooting guides provide detailed seasonal maintenance checklists.
Post-season storage preparation protects equipment during inactive periods. Fuel stabilization, thorough cleaning, and proper storage conditions prevent deterioration that leads to performance problems during subsequent seasons.
Advanced Troubleshooting Techniques
Systematic Diagnosis Methods
Effective troubleshooting follows logical sequences to identify root causes efficiently. Beginning with simple, common problems saves time and prevents unnecessary repairs. Air filter inspection, blade condition assessment, and fuel quality evaluation address most bogging issues quickly.
Advanced diagnostic techniques include compression testing, carburetor flow measurement, and electrical system analysis. These procedures require specialized tools and knowledge but provide definitive answers when basic troubleshooting proves insufficient.
Professional Service Considerations
Complex problems may require professional diagnosis and repair. Engine starting problems often indicate internal engine issues beyond typical DIY repair capabilities. Professional service ensures proper diagnosis and prevents costly mistakes from improper repairs.
Warranty considerations affect repair decisions significantly. Professional service maintains warranty coverage while ensuring proper repair procedures. DIY repairs may void warranties and create additional problems if performed incorrectly.
Brand-Specific Considerations
Common Brand Issues
Different manufacturers exhibit specific patterns in bogging problems. Husqvarna zero turn problems often involve PTO engagement issues, while Cub Cadet steering problems may compound cutting difficulties.
Understanding brand-specific issues helps focus troubleshooting efforts effectively. Manufacturer service bulletins often address known problems and provide specific solutions for common issues.
Parts Availability and Support
OEM parts ensure proper fit and performance compared to aftermarket alternatives. However, quality aftermarket parts may provide cost-effective solutions for older equipment where OEM parts become expensive or unavailable.
Dealer support varies significantly between brands and locations. Establishing relationships with knowledgeable dealers provides valuable resources for parts, service, and technical support throughout equipment ownership.
Frequently Asked Questions
Why does my zero turn mower bog down only in thick grass? Thick grass creates higher cutting resistance, demanding more engine power. If your mower bogs down only in dense conditions, the engine likely operates at its power limit. Solutions include raising deck height, ensuring sharp blades, and checking air filter condition for optimal performance.
Can bad fuel cause my mower to bog down when cutting? Yes, contaminated or old fuel significantly affects engine performance under load. Ethanol-blended fuels attract moisture and create deposits that restrict fuel flow precisely when engines need maximum fuel delivery. Always use fresh fuel and appropriate stabilizers for optimal performance.
How often should I sharpen zero turn mower blades to prevent bogging? Blade sharpening frequency depends on usage conditions and grass types. Commercial operators typically sharpen blades every 25-50 hours, while residential users may extend to 50-100 hours. Sharp blades reduce cutting resistance dramatically, preventing unnecessary engine load.
Will a clogged air filter cause bogging during cutting operations? Absolutely. Restricted air filters prevent proper air-fuel mixture, reducing engine power significantly during high-demand cutting. Air filters should be inspected every 25 hours and replaced when showing signs of restriction or damage.
Why does my mower bog down more when mulching compared to side discharge? Mulching decks require additional power to circulate clippings within the enclosed cutting chamber. This extra load can exceed engine capacity in thick grass conditions. Consider switching to side discharge during challenging cutting conditions to reduce engine load.
Can carburetor problems cause intermittent bogging issues? Yes, dirty or improperly adjusted carburetors often cause intermittent bogging, especially during transitions from idle to full-load cutting. Complete carburetor cleaning and proper adjustment typically resolve these fuel delivery issues.
Should I attempt DIY repairs for bogging problems or seek professional service? Basic maintenance like air filter replacement and blade sharpening can be performed by most owners. However, complex carburetor work or internal engine problems require professional diagnosis and repair to prevent costly mistakes and maintain warranty coverage.
Final Words
Zero turn mower bogging issues during cutting operations stem from preventable maintenance oversights in most cases. Regular air filter replacement, blade maintenance, and proper fuel system care eliminate the majority of power loss problems. When your zero turn mower bogs down when cutting grass, systematic troubleshooting beginning with these common causes provides the fastest path to restored performance.
Professional service becomes necessary when basic maintenance fails to resolve bogging issues, particularly for complex fuel system or internal engine problems. Investing in proper maintenance prevents costly repairs while ensuring your zero turn mower delivers consistent, reliable performance across all cutting conditions. Take action today by implementing a regular maintenance schedule that keeps your equipment operating at peak efficiency.