· Small Engine Repair · 12 min read
Kohler Engine Only Starts With Starter Fluid
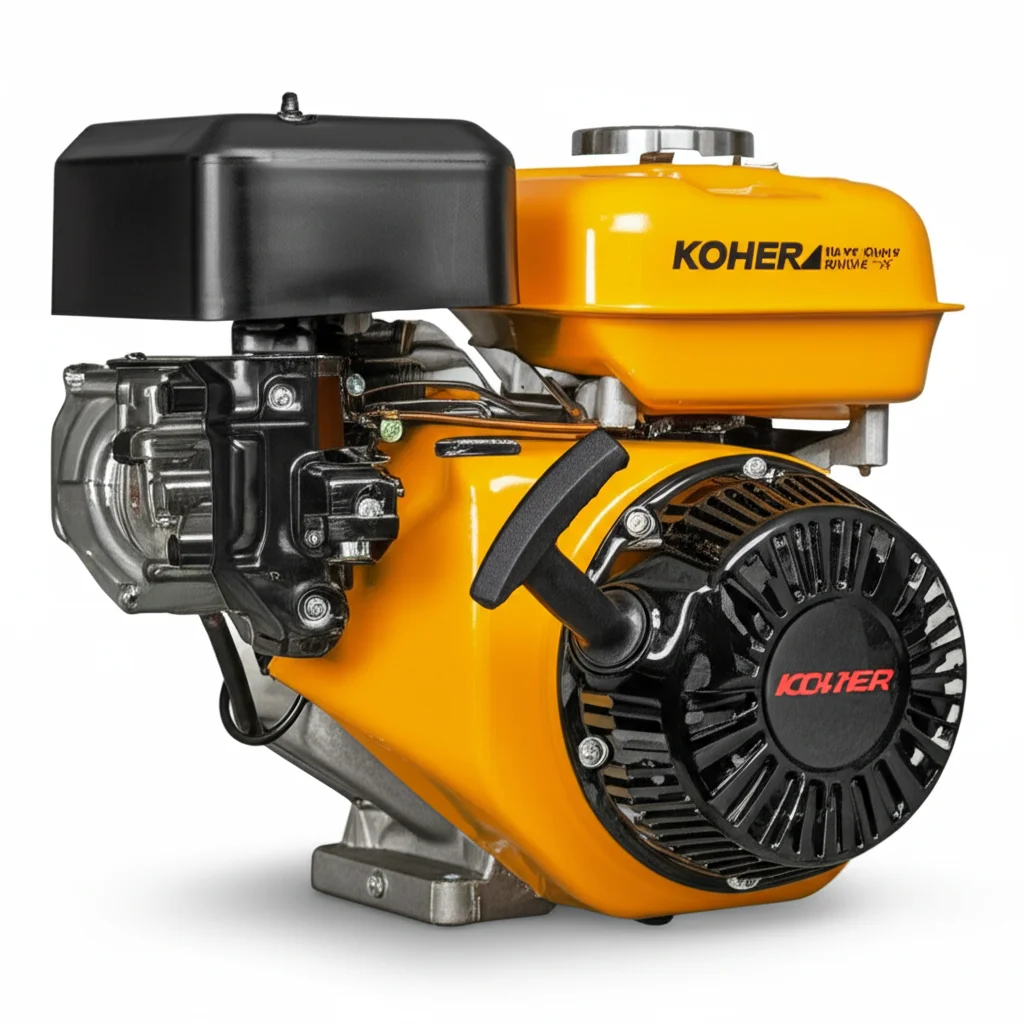
Kohler Engine Only Starts With Starter Fluid: Complete Troubleshooting Guide
If your Kohler engine only starts with starter fluid, you’re dealing with a fuel delivery problem that prevents proper combustion during startup.
This common issue typically stems from carburetor problems, fuel system blockages, or air intake restrictions that disrupt the engine’s ability to create the right fuel-air mixture for ignition.
Key Takeaways
• Carburetor cleaning resolves 80% of starter fluid dependency issues
• Fuel system inspection identifies blockages in lines, filters, and tank
• Air intake maintenance ensures proper airflow for combustion
• Choke adjustment helps create the rich mixture needed for cold starts
• Regular maintenance prevents most starting problems from developing
Quick Answer: When a Kohler engine only starts with starter fluid, it indicates insufficient fuel reaching the combustion chamber during startup, usually caused by a dirty carburetor, clogged fuel system, or improper choke operation.
Understanding Why Kohler Engines Need Starter Fluid
When your Kohler engine requires starter fluid to fire up, it’s essentially telling you that the normal fuel delivery system isn’t providing enough combustible mixture to the cylinder. Starter fluid contains highly volatile compounds that ignite easily, compensating for the inadequate fuel-air mixture your engine is receiving.
This dependency on starter fluid isn’t just inconvenient—it’s a symptom of underlying mechanical issues that will worsen over time if left unaddressed. Understanding the root causes helps you implement the right solution and prevent future occurrences.
The most common culprits include carburetor problems, fuel system blockages, and air intake issues. Each of these components plays a crucial role in creating the proper mixture needed for combustion, and when any one fails, your engine struggles to start normally.
Similar issues affect other small engines, and understanding engine starts with starter fluid but won’t stay running scenarios can provide additional insights into fuel delivery problems.
Common Causes of Starter Fluid Dependency
Carburetor Issues
The carburetor serves as your engine’s mixing chamber, blending fuel and air in precise ratios. When it becomes dirty or clogged, this delicate balance gets disrupted. Gum deposits, varnish buildup, and debris can block crucial passages, preventing fuel from reaching the combustion chamber in adequate quantities.
Old fuel sitting in the carburetor bowl often creates these blockages. Ethanol-blended gasoline is particularly problematic, as it attracts moisture and forms corrosive compounds that damage internal carburetor components. These deposits can completely obstruct jets and passages, making normal starting impossible.
Carburetor float problems also contribute to starting difficulties. If the float sticks or the needle valve fails, fuel flow becomes inconsistent, leaving insufficient fuel available during startup attempts.
Fuel System Problems
Your Kohler engine’s fuel system includes the tank, fuel lines, filter, and pump (if equipped). Blockages anywhere in this system reduce fuel flow to the carburetor, creating the same symptoms as carburetor problems.
Fuel filters are common failure points, especially when they haven’t been changed regularly. A partially clogged filter may allow enough fuel through for running but insufficient flow for starting. Water contamination in the fuel tank can also create starting problems, as water doesn’t burn and dilutes the available fuel.
Fuel line restrictions, whether from kinks, clogs, or collapsed lines, prevent adequate fuel delivery. These problems often develop gradually, making them difficult to notice until starting becomes impossible without assistance.
Air Intake Restrictions
While fuel problems get most attention, air intake issues can create identical symptoms. Your engine needs proper airflow to create combustible mixtures, and restrictions in the air cleaner or intake system disrupt this process.
Dirty air filters are the most common air intake problem. When filters become clogged with debris, grass clippings, or oil, they restrict airflow to the carburetor. This creates an overly rich mixture that’s difficult to ignite during startup.
Intake manifold leaks can also cause starting problems by allowing unmetered air into the system. These leaks disrupt the carburetor’s ability to maintain proper fuel-air ratios, particularly during the critical startup phase.
Understanding Kohler lawn mower engine surging issues can help identify intake problems that might affect starting performance.
Step-by-Step Troubleshooting Process
Initial Inspection
Begin your diagnosis by checking the most accessible components first. Remove the air filter and inspect its condition. A severely dirty or oil-soaked filter indicates maintenance neglect and likely contributes to your starting problems.
Check fuel levels and quality next. Old, contaminated, or water-laden fuel should be drained and replaced. Look for signs of fuel system problems like rust in the tank, debris in fuel lines, or damaged components.
Examine the choke mechanism to ensure it’s operating properly. The choke should close completely when the engine is cold and open gradually as the engine warms. Manual chokes should move freely without binding or sticking.
Carburetor Diagnosis
Remove the carburetor bowl to inspect internal conditions. Look for water, debris, or gummy deposits that indicate fuel system contamination. Clean fuel should be relatively clear, while contaminated fuel appears cloudy or contains visible particles.
Check the carburetor float for proper operation. It should move freely and maintain proper fuel levels in the bowl. Stuck floats or damaged needle valves prevent normal fuel delivery during startup attempts.
Inspect carburetor jets and passages for blockages. These tiny openings are easily clogged by fuel deposits and require careful cleaning to restore proper function. Use appropriate cleaning solutions and avoid damaging delicate components.
Fuel System Testing
Test fuel flow by disconnecting the fuel line at the carburetor and checking flow rate. Fuel should flow steadily when the tank is full and slow to a trickle as the tank empties. Weak or intermittent flow indicates system restrictions.
Replace the fuel filter if it appears dirty or hasn’t been changed recently. Fuel filters are inexpensive insurance against fuel system problems and should be replaced according to manufacturer recommendations.
Check fuel pump operation on equipped models. Pump diaphragms can deteriorate over time, reducing fuel delivery pressure and volume. Testing requires specialized equipment, but symptoms like weak fuel flow or pressure loss indicate pump problems.
Carburetor Cleaning and Repair
Disassembly Process
Proper carburetor cleaning requires complete disassembly to access all internal components. Document the disassembly process with photos to ensure correct reassembly. Remove all gaskets, O-rings, and seals, as these typically need replacement during rebuilding.
Pay special attention to small components like jets, needles, and springs. These parts are easily lost and difficult to replace individually. Keep them organized in labeled containers to prevent confusion during reassembly.
Mark the positions of adjustable components like mixture screws and idle adjustments. These settings affect engine performance and should be returned to their original positions unless adjustment is specifically needed.
Cleaning Techniques
Use appropriate carburetor cleaning solvents to dissolve fuel deposits and varnish. Avoid harsh chemicals that might damage rubber or plastic components. Ultrasonic cleaners provide excellent results but aren’t necessary for most home repairs.
Clean all passages with appropriate tools, using compressed air to verify that all blockages are removed. Pay particular attention to main jets, pilot jets, and accelerator pump circuits, as these are critical for proper fuel delivery.
Inspect and clean the carburetor bowl thoroughly. Remove all debris and ensure the bowl gasket surfaces are clean and smooth. Damaged gasket surfaces can cause fuel leaks and starting problems.
Reassembly and Adjustment
Install new gaskets and seals during reassembly to prevent fuel leaks and air infiltration. Tighten fasteners to specified torque values to avoid damage while ensuring proper sealing.
Set initial mixture and idle adjustments according to manufacturer specifications. These settings provide a baseline for fine-tuning once the engine is running. Final adjustments may be needed to optimize performance.
Test the completed assembly for proper operation before installation. Check float level, needle valve sealing, and throttle operation to ensure everything functions correctly.
For complex carburetor issues, consider consulting resources about 25 HP Kohler Command Pro engine problems for additional troubleshooting guidance.
Fuel System Maintenance
Tank and Line Service
Clean the fuel tank periodically to remove water and debris accumulation. Water settles to the bottom of tanks and can be drained through petcocks or siphoned out during tank removal. Use appropriate cleaning solvents to remove varnish deposits from tank walls.
Replace fuel lines that show signs of deterioration, cracking, or internal collapse. Ethanol fuels are particularly hard on rubber components, causing premature failure of fuel system parts. Use ethanol-resistant materials for replacements.
Install inline fuel filters if your system doesn’t include them. Filters provide additional protection against contamination and are easily replaceable during routine maintenance intervals.
Filter Replacement
Replace fuel filters according to manufacturer recommendations or when they appear dirty. Clogged filters restrict fuel flow and can cause starting problems that mimic carburetor issues.
Use OEM or equivalent quality filters to ensure proper fit and filtration. Cheap aftermarket filters may not provide adequate protection or may fail prematurely, causing additional problems.
Install filters with proper flow direction orientation. Reversed filters can reduce filtration effectiveness and may contribute to fuel system problems.
Pump Maintenance
Inspect fuel pump diaphragms annually on equipped engines. Cracked or deteriorated diaphragms reduce pumping capacity and can cause starting difficulties. Replace complete pump assemblies rather than attempting diaphragm-only repairs.
Check fuel pump mounting and ensure all connections are secure. Loose connections can cause air leaks that reduce pump efficiency and fuel delivery.
Test pump pressure and volume output if starting problems persist after other repairs. Weak pumps may provide enough fuel for idle operation but insufficient flow for starting under load.
Air Intake System Solutions
Filter Maintenance
Clean or replace air filters regularly to maintain proper airflow. Paper filters should be replaced when dirty, while foam filters can be cleaned with soap and water, then re-oiled before installation.
Inspect filter housing for cracks or damage that might allow unfiltered air into the engine. Damaged housings should be repaired or replaced to prevent engine damage from contaminants.
Ensure proper filter installation with all sealing surfaces properly seated. Improperly installed filters allow dust bypass that can damage internal engine components.
Intake System Inspection
Check intake manifold connections for air leaks that can disrupt fuel mixture ratios. Use carburetor cleaner spray around suspected leak areas while the engine is running—RPM changes indicate leak locations.
Inspect choke mechanisms for proper operation and adjustment. Chokes that don’t close completely prevent rich mixture formation needed for cold starting, while chokes that stick closed cause rich running conditions.
Verify that all intake system components are properly secured and sealed. Loose connections allow unmeasured air into the system, affecting fuel mixture and starting performance.
Understanding related issues like Briggs and Stratton lawn mower starts then dies can provide insights into similar air-fuel mixture problems across different engine brands.
Prevention and Maintenance Tips
Fuel Quality Management
Use fresh fuel and avoid storing gasoline for extended periods without stabilizers. Ethanol-blended fuels deteriorate quickly and create deposits that cause starting problems. Add fuel stabilizer to stored fuel to prevent degradation.
Drain fuel systems before long-term storage to prevent fuel deterioration in carburetor components. Run engines dry or use fuel shut-off valves to isolate carburetors from fuel supplies during storage periods.
Consider using ethanol-free fuel when available, as it stores better and causes fewer problems in small engine fuel systems. While more expensive, it often pays for itself in reduced maintenance costs.
Regular Service Schedule
Establish routine maintenance intervals that include fuel filter replacement, air filter service, and carburetor inspection. Preventive maintenance prevents most starting problems from developing.
Clean carburetor bowls annually or when fuel quality is questionable. This simple maintenance step prevents most fuel-related starting problems and extends carburetor service life.
Inspect and clean cooling fins, which affect engine temperature and starting characteristics. Overheating engines often develop starting problems that mimic fuel system issues.
Regular maintenance prevents many issues found in Cub Cadet EFI engine problems, demonstrating the importance of preventive care across all engine types.
Storage Considerations
Prepare engines properly for seasonal storage to prevent starting problems when returned to service. This includes fuel stabilization, oil changes, and protecting exposed metal surfaces from corrosion.
Store equipment in dry locations to prevent moisture-related problems in fuel and electrical systems. Humidity accelerates fuel deterioration and promotes corrosion of metal components.
Consider periodic operation during storage periods to maintain fuel system function and prevent component deterioration. Monthly startup and operation helps identify developing problems before they become serious.
Frequently Asked Questions
Why do I have to start my mower with starter fluid? Your mower requires starter fluid because the normal fuel delivery system isn’t providing adequate fuel to the combustion chamber during startup. This typically indicates carburetor problems, fuel system blockages, or air intake restrictions that prevent proper fuel-air mixture formation.
Why does my engine need starting fluid to start? Engines need starting fluid when their fuel systems can’t deliver enough combustible mixture for ignition. Starting fluid contains highly volatile compounds that ignite easily, compensating for insufficient fuel delivery from a malfunctioning carburetor or clogged fuel system.
What replaces starting fluid? While starting fluid can be temporarily replaced with carburetor cleaner or WD-40, the proper solution is fixing the underlying fuel delivery problem. Clean the carburetor, replace fuel filters, and ensure proper air intake function to eliminate starter fluid dependency.
Will starter fluid help a bad starter? Starter fluid won’t help a bad electric starter motor, as it only aids combustion, not cranking. If your engine cranks but won’t start, starter fluid may help identify fuel system problems. However, mechanical starter issues require starter motor repair or replacement.
Is starting fluid bad for small engines? Occasional starter fluid use won’t damage engines, but regular dependency indicates problems that should be addressed. Excessive use can wash cylinder walls clean of oil, potentially causing wear. Fix fuel delivery problems rather than relying on starter fluid long-term.
How often should I clean my Kohler engine carburetor? Clean your Kohler carburetor annually or whenever you notice starting problems, rough running, or poor performance. Engines using ethanol-blended fuels may require more frequent cleaning due to increased deposit formation and component deterioration.
Can bad fuel cause starter fluid dependency? Yes, contaminated, old, or water-laden fuel commonly causes starting problems that require starter fluid assistance. Old fuel forms deposits that clog carburetor passages, while water contamination prevents proper combustion. Always use fresh, clean fuel for optimal performance.
Final Words
When your Kohler engine only starts with starter fluid, systematic troubleshooting will identify and resolve the underlying fuel delivery problems causing this frustrating symptom. Most cases involve carburetor cleaning, fuel system maintenance, or air intake service—all manageable repairs for DIY mechanics with basic tools and patience.
Regular maintenance prevents most starting problems from developing, making prevention far easier than diagnosis and repair. Establish routine service intervals, use quality fuel, and address problems promptly to keep your Kohler engine starting reliably without chemical assistance.
Don’t let starter fluid dependency continue—take action to restore your engine’s normal starting capability and enjoy reliable operation for years to come. For additional engine troubleshooting resources and maintenance guides, explore our comprehensive collection of small engine repair solutions.