· Troubleshooting · 17 min read
Husqvarna Safety Switch Bypass
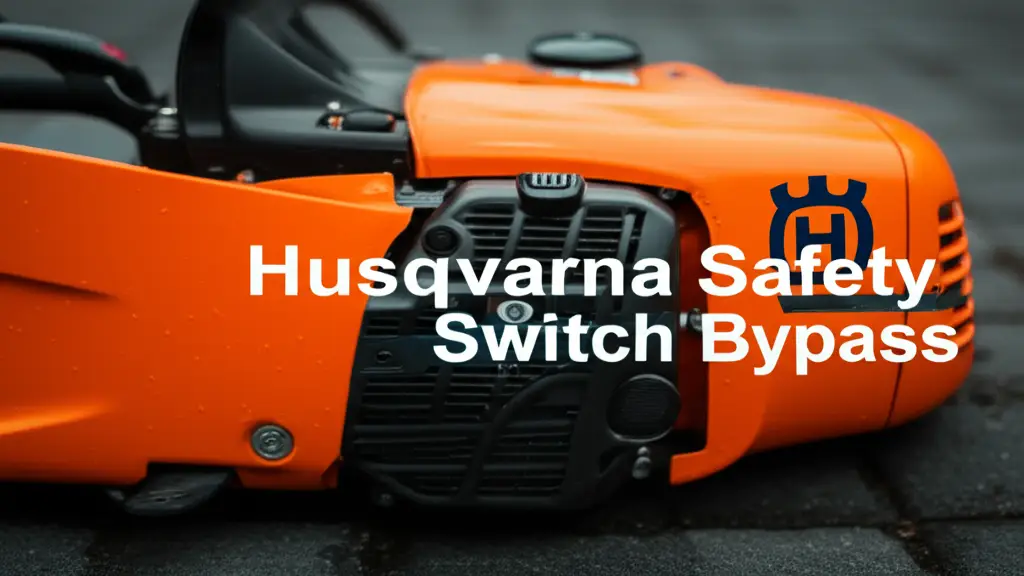
Husqvarna Safety Switch Bypass: Is It Worth the Risk?
Have you ever been frustrated by a Husqvarna mower that won’t start, seemingly for no reason? Often, the culprit is a faulty or finicky safety switch. It’s tempting to consider a Husqvarna safety switch bypass to get back to work quickly.
However, bypassing these crucial safety features isn’t a decision to take lightly. This article will explore the reasons why you might be considering a bypass, the potential dangers involved, troubleshooting steps, and safer alternatives to keep you and your mower operating correctly.
We’ll cover everything from seat switches to brake switches, helping you understand the full picture.
Takeaway:
- Husqvarna safety switches are crucial safety features designed to prevent severe injuries and fatalities.
- Bypassing these switches, even temporarily, introduces extreme hazards, voids warranties, and incurs significant legal and financial liabilities.
- Proper diagnosis and repair of faulty safety switches are the only safe and responsible solutions.
What is a Husqvarna Safety Switch Bypass?
A Husqvarna safety switch bypass refers to intentionally disabling or circumventing one or more of the mower’s built-in safety interlock switches.
This action allows the machine to operate under conditions that the manufacturer designed to be unsafe, such as running without an operator in the seat or with blades engaged in reverse. This practice is highly dangerous and strongly discouraged.
Diagnosing the Problem: Symptoms of a Faulty Safety Switch
When a Husqvarna mower malfunctions, particularly with starting or unexpected shutdowns, a faulty safety switch is often suspected.
However, it is important to recognize the specific symptoms that point to these components and to differentiate them from other common issues.
Recognizing a Faulty Safety Switch
Several key indicators suggest that a safety switch might be malfunctioning:
Mower won’t start or crank:
This is one of the most common and frustrating symptoms. If the engine fails to respond when the key is turned, or if it cranks but does not fire up, a safety switch may be preventing the starter solenoid from receiving its necessary signal.
The mower’s electrical system is designed to prevent starting if any safety interlock condition (like the parking brake not being engaged or the cutting deck being lowered) is not met.
Engine dies when engaging blades/arms:
If the mower starts and runs, but then abruptly stalls or shuts off as soon as the PTO (blade engagement) is activated, it strongly suggests an issue with the PTO switch or a related interlock in that circuit.
Intermittent cutting or stalling:
A partially failing safety switch, especially the seat switch, can lead to erratic behavior.
The mower might cut in and out randomly while operating, indicating that the switch is degrading but has not completely failed.
This can be particularly frustrating for operators trying to complete a task.
Mower dies when shifting into reverse:
If the engine stalls immediately upon shifting the transmission into reverse, particularly when the blades are engaged, the reverse safety switch is a likely culprit. This safety feature is designed to prevent unintended blade operation in reverse.
Beyond the Switch: Other Common Starting and Running Issues
While safety switches are frequent sources of trouble, it is crucial to consider other common issues that can produce similar symptoms, especially a “no start” condition. A comprehensive diagnostic approach prevents misdiagnosis and unnecessary repairs.
Battery problems:
A dead, low-charged, or corroded battery is a very common reason for a mower not starting.
Symptoms include a complete lack of response when turning the key, slow cranking, or only a clicking sound from the starter solenoid.
Always check battery terminals for corrosion and ensure connections are clean and tight.
Fuel system issues:
Problems with the fuel delivery system can prevent the engine from firing. This includes clogged fuel lines, a dirty fuel filter, or an obstructed vent on the fuel cap, all of which can restrict fuel flow to the carburetor.
Spark plug and ignition system faults:
Worn, dirty, or fouled spark plugs can prevent proper ignition, leading to a no-start condition or rough running.
The ignition switch itself can also fail, preventing power from reaching critical starting components.
Blown fuses or faulty relays:
Fuses act as sacrificial components, protecting the electrical system from overcurrents.
A blown fuse can interrupt power to various circuits, including the starting circuit, leading to a no-start condition.
Similarly, electrical relays, which are used to control circuits, can fail and prevent components from receiving power.
The multitude of potential causes for a “no start” condition, ranging from simple battery issues to complex electrical faults involving multiple safety switches, underscores the importance of a systematic diagnostic process. Many factors—battery charge, fuel delivery, spark plugs, fuses, relays, and various safety interlocks—can all contribute to a mower failing to start.
This means that jumping to conclusions about a single safety switch being the problem, or attempting a bypass without proper investigation, is often inefficient and potentially misleading.
A fault in one area, such as a corroded fuse, can manifest symptoms that mimic a safety switch problem.
Therefore, a methodical troubleshooting approach is paramount. Instead of immediately assuming a safety switch is faulty and attempting a bypass, individuals should systematically check all potential culprits.
This process should ideally begin with the easiest and most common issues, such as verifying battery charge, checking fuel levels, and inspecting fuses, before proceeding to more intricate electrical diagnostics involving individual switches.
This disciplined approach not only helps in accurately pinpointing the root cause but also prevents unnecessary parts replacement and mitigates the risks associated with incorrect bypass attempts.
The Solution: Accurate Diagnosis and Proper Repair
Accurately diagnosing a faulty safety switch requires a systematic approach and the right tools. Guessing can lead to frustration, wasted time, and unnecessary expense.
Essential Tools: The Multimeter and How to Use It for Continuity Testing
The most indispensable tool for diagnosing electrical issues in a lawn mower is a multimeter.
This versatile device allows for various electrical tests, but for safety switches, its continuity setting is key.
This setting typically produces an audible beep when a complete circuit (continuity) is detected, making it easy to identify whether a switch is opening or closing as expected.
To test for continuity, the multimeter’s probes are touched to the switch’s contacts. A properly functioning switch will show continuity when engaged and no continuity when disengaged, or vice-versa, depending on whether it’s a Normally Open (NO) or Normally Closed (NC) type.
If the switch fails to show the expected change in continuity, it indicates a fault and likely needs replacement.
Step-by-Step Testing Procedures for Each Switch Type
Before performing any electrical tests or repairs, always prioritize safety: turn off the engine, remove the ignition key, and disconnect the battery cables to prevent accidental startup or electrical shock.
- Testing the Seat Safety Switch:
- Location: The seat safety switch is typically found directly underneath the operator’s seat. Access may require tilting or unbolting the seat.
- Wiring: These switches can have either 2-wire or 4-wire configurations. For 4-wire switches, a multimeter should be used to check continuity across different pairs of terminals both when the seat is occupied (simulated by pressing the switch plunger) and when it is unoccupied. Often, two side-by-side wires are paired.
- “Shorting Bars” and Anti-Tamper Features: It is crucial to understand that many Husqvarna (and other manufacturers like MTD) seat switch connectors incorporate an “anti-tamper” or “shorting bar” feature. This metal fork-like piece is designed to short out the circuit and kill the engine if the seat switch is simply unplugged. For diagnostic testing purposes only, this shorting bar may need to be carefully removed from the connector, or insulated (e.g., with small pieces of zip tie or toothpick), to simulate a working switch when the main switch is disconnected. This allows for a proper continuity test of the switch itself without the anti-tamper feature interfering.
- Testing the PTO Safety Switch:
- Location: The PTO switch is usually located on the dashboard or near the PTO engagement lever.
- Procedure: With the multimeter set to continuity, touch the probes to the switch contacts. Engage and disengage the PTO switch. A functional PTO switch should show a clear change in continuity (from open to closed, or closed to open) between its engaged and disengaged states. If it maintains continuity in both states, or no continuity in either, it is faulty. Many PTO switches are Normally Closed (NC) when the PTO is off.
- Testing the Brake Safety Switch:
- Location: This switch is typically found near the brake pedal, often mounted in a position where it is activated when the pedal is depressed. It might even be mounted upside down in some models, making access challenging.
- Procedure: Test continuity across the switch terminals while the brake pedal is pressed down and then released. A working brake switch will show a distinct change in circuit state (continuity or no continuity) as the pedal is operated.
- Testing the Reverse Safety Switch:
- Location: The reverse safety switch is commonly situated on top of the transmission or near the shift lever mechanism.
- Procedure: Use the multimeter to test for continuity as the shift mechanism is moved between neutral, forward, and reverse positions. The switch should exhibit a change in its electrical state (e.g., opening or closing a circuit) when the mower is shifted into reverse.
- Testing the Neutral Start Safety Switch:
- Function: These switches are designed to ensure that the mower can only be started when the transmission is in the neutral position, preventing unexpected lurching.
- Procedure: Test continuity across the switch terminals with the transmission in neutral and then in various gear positions. The switch should only allow the starting circuit to be completed (or opened, depending on its design) when the transmission is correctly in neutral.
To aid in the diagnostic process, the following table provides a quick reference for Husqvarna safety switch locations, functions, typical electrical behavior, and common failure symptoms:
Switch Type | Common Location | Function | Typical Behavior (NO/NC) | Expected Multimeter Reading (Engaged/Active) | Expected Multimeter Reading (Disengaged/Inactive) | Common Symptoms of Failure |
---|---|---|---|---|---|---|
Seat | Under seat | Operator presence | Varies (NO or NC) | Continuity (if NO), No Continuity (if NC) | No Continuity (if NO), Continuity (if NC) | Won’t start, Engine dies when leaving seat, Intermittent stalling |
PTO | Dashboard/Control Panel | Blade engagement | Often NC | No Continuity (when engaged) | Continuity (when disengaged) | Engine dies when engaging blades, Blades won’t engage |
Brake | Near brake pedal | Starting interlock | Varies (NO or NC) | Continuity (when pressed) | No Continuity (when released) | Won’t start (even with brake pressed) |
Reverse | On transmission/Shift lever | Reverse lockout | Varies (NO or NC) | Change in state (e.g., opens circuit) | Normal state (e.g., closed circuit) | Engine dies in reverse, Blades operate in reverse |
Neutral Start | Transmission/Shift mechanism | Prevents starting in gear | Varies (NO or NC) | Continuity (in neutral) | No Continuity (in gear) | Won’t start (even in neutral) |
Replacing a Faulty Safety Switch
Once a faulty safety switch has been definitively identified through testing, replacement is the appropriate solution.
Importance of OEM parts:
Always recommend using genuine OEM (Original Equipment Manufacturer) parts for replacements.
OEM parts are designed specifically for the Husqvarna model, ensuring proper fit, function, and compatibility with the mower’s intricate electrical system.
Aftermarket “knock-off” parts, while sometimes cheaper, can lead to further issues or inconsistent performance. Using OEM parts also helps maintain any remaining manufacturer warranty.
General replacement steps:
- Safety First: Turn off the engine, remove the key from the ignition, and disconnect the battery’s negative terminal to prevent accidental startup or electrical hazards.
- Locate and Access: Identify the precise location of the faulty switch. This may require removing panels or tilting components, depending on the switch type and mower model.
- Disconnect Wiring: Carefully disconnect the electrical wiring harness from the old switch. Pay attention to how the wires are connected, as some harnesses are designed to attach in only one specific way.
- Remove Old Switch: Unclip or unscrew the old switch from its mounting location.
- Install New Switch: Position the new switch in the same location and snap or screw it securely into place. Reconnect the wiring harness, ensuring all connections are firm and correctly aligned.
- Test Functionality: Reconnect the battery. Before operating the mower fully, perform a thorough test of the new switch’s functionality to ensure it operates as expected and resolves the original issue.
Consequences of a Bypass: The Steep Price of Disabling Safety Features
The decision to bypass a Husqvarna mower’s safety switches carries a steep price, extending far beyond immediate operational convenience.
The consequences encompass catastrophic safety hazards, severe legal and insurance ramifications, potential damage to the mower’s electrical system, and a significant reduction in its resale value.
Catastrophic Safety Hazards
The most immediate and dire consequence of disabling safety features is the dramatically increased risk of severe injury or death.
Lawn Mower accidents are tragically common, with approximately 90 fatalities occurring annually, often due to riding mowers overturning and crushing operators, or machines running over victims.
Injuries are frequently catastrophic, including finger, toe, hand, and foot amputations, as well as deep cuts and lacerations that require emergency surgery and can result in permanent disability.
Mower blades, spinning at speeds up to 3,000 RPM, are capable of severing limbs instantly.
Bypassing the seat safety switch, for instance, means the mower will continue to operate even if the driver falls off, potentially running over or crushing them. This is a particular concern on slopes or uneven terrain.
Similarly, disabling the reverse safety switch removes a critical safeguard against backing over individuals, especially young children who may be unseen behind the mower.
Beyond direct contact, mowers can throw objects at speeds up to 200 mph, posing a significant projectile hazard.
Operators are also at risk of burns from hot engine parts and long-term noise-induced hearing loss if proper protection is not used.
To further underscore the risks, the following table summarizes common temporary bypass methods and their associated severe safety warnings:
Switch Type | Bypass Method (Temporary/Diagnostic Only) | Prominent Safety Warning | Legal/Warranty Risk |
---|---|---|---|
Seat Safety Switch | Remove shorting bar/metal fork piece from connector; Zip-tie/tape plunger; Place object (cardboard/cans) under seat. | EXTREME DANGER: Mower will operate without operator presence. High risk of severe injury, crushing, or death if operator falls off or dismounts with blades engaged. | Voids manufacturer warranty; Increases operator’s legal liability in case of accident. |
PTO Safety Switch | Jumper specific wires on harness (requires wiring diagram). | EXTREME DANGER: Blades can engage unexpectedly or remain engaged when operator dismounts. High risk of amputations or severe cuts. | Voids manufacturer warranty; Increases operator’s legal liability in case of accident. |
Reverse Safety Switch | Unplug wire from switch; Physically reposition switch out of the way. | EXTREME DANGER: Disables blade disengagement in reverse. Significantly increases risk of backing over individuals, especially children, leading to severe injury or death. | Voids manufacturer warranty; Increases operator’s legal liability in case of accident. |
Legal and Insurance Ramifications
The act of modifying a lawn mower’s safety features has profound legal and financial implications.
Manufacturers explicitly state that any attempt to bypass or disconnect safety features will likely void some or all of the product warranty.
This means that any future repairs, even for unrelated issues, would become the sole financial responsibility of the owner, negating the benefits of the original warranty.
More critically, disabling safety features dramatically increases the operator’s legal liability in the event of an accident.
Lawnmower injury cases often involve complex legal frameworks, including product liability, negligence, and premises liability.
While manufacturers can be held liable for injuries caused by design defects, manufacturing flaws, or inadequate warnings, this liability shifts significantly when the user modifies the equipment.
If an injury occurs with a bypassed safety switch, the responsibility would likely fall squarely on the operator due to their direct negligence in altering a safety device.
This also extends to homeowners insurance coverage. While homeowners insurance typically provides liability coverage for medical and legal expenses if someone not residing in the household is injured on the property by a lawn mower, this coverage can be jeopardized by modifications.
Insurance claims for accidents involving equipment with altered safety features may be denied. Policies often contain exclusions for damage or injury caused by the homeowner’s failure to conduct routine maintenance, neglect, or modifications to equipment.
A claim denial could leave the operator personally responsible for potentially catastrophic medical bills, legal fees, and damages.
This transforms a potential product liability case against the manufacturer into a direct negligence claim against the operator, highlighting that the financial and legal ramifications of a bypass far outweigh the perceived convenience.
Potential Electrical System Damage and Long-Term Issues
Beyond the immediate safety and legal risks, improperly bypassing a safety switch can inflict long-term damage on the mower’s electrical system.
These systems are designed with specific resistances and circuits, and altering them can lead to unintended consequences.
Connecting wires incorrectly or creating a permanent short circuit can cause electrical overloads, leading to blown fuses or, more severely, damage to other sensitive electrical components within the mower’s complex system.
A faulty bypass could introduce unforeseen electrical malfunctions, stressing components beyond their design limits and potentially leading to more expensive and intricate repairs down the line.
This could manifest as intermittent electrical issues, premature component failure, or even a complete breakdown of the mower’s electrical system.
Diminished Resale Value
Modifying a Husqvarna mower by bypassing or removing safety features also has a direct negative impact on its economic value. Such a mower will be significantly harder to sell in the used market.
Buyers are inherently wary of equipment with compromised safety features and potential underlying electrical issues that may have been introduced by the modification.
The general consensus in the used equipment market is that “a 100% stock vehicle will always sell for more than a modified one”.
This principle applies strongly to lawnmowers, which are often viewed as utilitarian appliances rather than collectible items. Modifications, particularly those that compromise safety, diminish the perceived quality, reliability, and, consequently, the market value of the equipment.
A mower with disabled safety features is explicitly less desirable and its market value will depreciate faster, if it can be sold at all.
This economic reality provides a compelling financial argument against permanent modification. The cost of a new, genuine OEM safety switch is typically modest, often ranging from $15 to $40.
This is negligible compared to the potential loss in resale value, which could amount to hundreds or even thousands of dollars depending on the mower’s original value.
When considering the potential for denied insurance claims or personal liability for accident-related costs, the perceived “savings” or convenience of a bypass quickly becomes a significant financial detriment.
The Responsible Path: Proper Troubleshooting, Repair, and Maintenance
Given the severe risks and liabilities associated with bypassing Husqvarna safety switches, the responsible and recommended course of action is always proper diagnosis, repair, and consistent maintenance.
Systematic Troubleshooting Approach
When a Husqvarna mower exhibits starting problems or unexpected shutdowns, a systematic troubleshooting approach is the most effective way to identify and resolve the issue.
Start with the simplest checks:
Before delving into complex electrical diagnostics, always begin with the basics. Check the fuel level, ensure the battery is fully charged and its terminals are clean and tight, inspect the spark plugs for fouling or damage, and verify that all fuses are intact.
Many issues that seem like safety switch problems are often resolved by addressing these fundamental components.
Isolate the problem component:
Once basic checks are cleared, use a multimeter to systematically test each suspected safety switch or electrical component.
This methodical approach helps pinpoint the exact fault rather than relying on guesswork, which can lead to unnecessary parts replacement and prolonged downtime.
Preventative Maintenance for Safety Switches and Electrical Systems
Proactive maintenance can significantly extend the life of safety switches and prevent many common electrical issues.
Regular inspections and cleaning:
Periodically perform visual checks of all accessible safety switches and their wiring for signs of wear, loose connections, corrosion, or physical damage.
Keep electrical connections clean and consider applying dielectric grease to prevent moisture intrusion and corrosion, which can lead to intermittent issues or complete failure.
Checking wiring for damage:
Inspect wiring harnesses for any signs of rubbing, chafing, bare spots, or damage from rodents.
Damaged wiring can cause short circuits, blown fuses, or intermittent electrical problems that mimic faulty switches.
Address any damaged wiring promptly by repairing or replacing the affected sections.
When to Seek Professional Help
While many troubleshooting and repair tasks can be performed by a knowledgeable DIYer, there are instances when professional assistance is strongly advised.
Complex electrical issues:
If the diagnostic process becomes too complex, or if the user is uncertain about interpreting wiring diagrams, multimeter readings, or the underlying electrical theory, it is best to consult a professional.
Modern mower electrical systems can be intricate, and misdiagnosis can lead to further damage.
Uncertainty about diagnosis or repair:
If basic troubleshooting does not resolve the problem, or if the user does not feel comfortable performing the necessary repair, taking the mower to a certified Husqvarna service center or a reputable small engine repair shop is the safest and most efficient course of action.
Attempting repairs beyond one’s skill level can lead to additional damage to the equipment, or worse, serious personal injury.
Professionals have specialized tools, training, and experience to diagnose and repair issues correctly and safely.