· Lawn Mower Maintenance · 7 min read
How To Fix The No Loop Signal On Husqvarna Automower
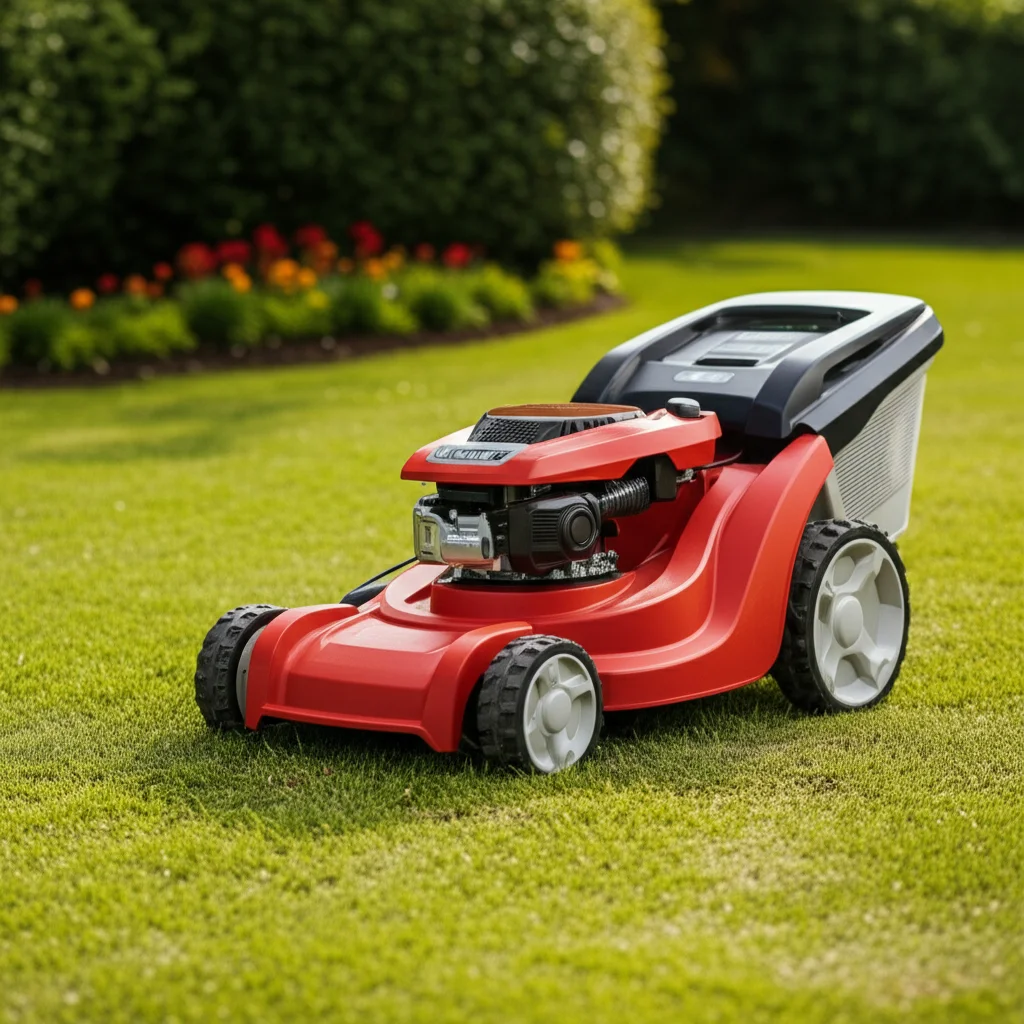
Diagnosing & Fixing Your Husqvarna Automower’s No Loop Signal
Have you been frustrated by your Husqvarna Automower displaying a “No Loop Signal” error? It’s a common issue, but thankfully, often a straightforward fix. This guide will walk you through the most likely causes and provide step-by-step instructions to get your robotic mower back on track. A strong loop signal is essential for your Automower to know where to mow and where not to mow, so let’s get it sorted! We’ll cover everything from checking the wire connections to identifying potential breaks in the perimeter wire.
Takeaway:
- Check the wire connections at the base station.
- Inspect the perimeter wire for breaks or damage.
- Ensure the base station is properly grounded.
- Test the loop signal strength with a multimeter.
- Consider interference from other electrical sources.
A “No Loop Signal” error means your Husqvarna Automower isn’t receiving the radio frequency emitted by the perimeter wire. This wire defines the area your mower is programmed to work within. Without this signal, the mower won’t operate for safety reasons. Let’s dive into how to resolve this issue.
1. Understanding the Loop Signal & Its Importance
The loop signal is the backbone of your Husqvarna Automower’s operation. It’s a low-voltage radio frequency transmitted through the perimeter wire you install around your lawn. This signal tells the mower where the boundaries of its mowing area are, preventing it from wandering onto roads, flowerbeds, or other areas you don’t want it to go. A consistent and strong signal is crucial for reliable performance. If the signal is weak or absent, the mower will display the “No Loop Signal” error and refuse to start.
Think of it like an invisible fence for your robotic mower. Maintaining this “fence” is key to a hassle-free mowing experience. Sometimes, simple things like a loose connection can disrupt this signal. You might also find that weather conditions or nearby electrical interference can play a role. If you’re looking for ways to keep your entire home clean, check out this guide on how-to-clean-luxury-vinyl-plank-flooring for maintaining other areas of your property.
2. Checking Connections at the Base Station
The base station is where the loop signal originates. It’s the first place to check when you encounter a “No Loop Signal” error. Start by visually inspecting the wire connections to the base station terminals. Ensure they are secure, clean, and free from corrosion. Loose or corroded connections can significantly weaken the signal.
Here’s what to do:
- Power off the base station: Disconnect the power supply for safety.
- Inspect the terminals: Look for any signs of rust, dirt, or loose wires.
- Tighten connections: Gently tighten any loose screws or clamps.
- Clean the terminals: If you see corrosion, carefully clean the terminals with a wire brush or sandpaper.
- Reconnect and test: Power on the base station and check if the error persists.
Sometimes, the wire itself can be damaged right at the point where it enters the base station. A small break or fray can be enough to disrupt the signal. If you’re dealing with other cleaning tasks around the house, you might find this article on how-to-clean-a-3ds-screen helpful.
3. Inspecting the Perimeter Wire for Damage
The perimeter wire is vulnerable to damage from various sources, including lawnmowers, gardening tools, animals, and even settling ground. A break in the wire will immediately interrupt the loop signal. A thorough inspection is essential.
- Visual Inspection: Walk the entire perimeter of your lawn, carefully examining the wire for any visible breaks, cuts, or exposed copper.
- Look for Buried Damage: Areas where the wire is buried are more susceptible to damage from digging or root growth. Probe the ground gently with a screwdriver to check for breaks.
- Use a Wire Tester: A dedicated loop wire tester (available from Husqvarna or other retailers) can quickly identify breaks in the wire. These testers send a signal through the wire and alert you to any interruptions.
- Repairing Breaks: If you find a break, use waterproof wire connectors specifically designed for low-voltage outdoor use to repair it. Ensure the connection is secure and well-insulated.
Remember, even a tiny nick in the wire can cause problems. Regularly checking the wire, especially after landscaping work, can prevent these issues. If you’re looking for a quick fix for another appliance, consider this guide on quick-fix-shark-steam-mop-not-steaming.
4. Checking the Grounding of the Base Station
Proper grounding is crucial for a stable loop signal. The base station needs a good earth connection to function correctly. If the grounding is poor, it can lead to signal interference and the “No Loop Signal” error.
- Locate the Grounding Point: The base station should have a designated grounding point, usually a screw terminal.
- Inspect the Ground Wire: Ensure the ground wire is securely connected to a suitable grounding rod or a properly grounded electrical outlet.
- Check Ground Resistance: Use a multimeter to measure the ground resistance. It should be as low as possible (ideally below 5 ohms).
- Improve Grounding: If the ground resistance is high, consider installing a new grounding rod or improving the connection to an existing one.
A poor ground can also create electrical noise that interferes with the loop signal. Ensuring a solid ground connection is a simple step that can often resolve the issue. If you’re dealing with other household maintenance, you might find this article on how-to-fix-squeaky-hardwood-floors-with-baby-powder helpful.
5. Testing Loop Signal Strength with a Multimeter
If you’ve checked the connections and the wire and the problem persists, use a multimeter to test the loop signal strength. This will help you pinpoint the location of the issue.
- Set the Multimeter: Set your multimeter to measure AC voltage.
- Connect the Probes: Connect the multimeter probes to the loop wire terminals at the base station.
- Read the Voltage: A healthy loop signal should typically read between 18-24 volts AC. If the voltage is significantly lower, it indicates a problem.
- Test at Different Points: Test the voltage at various points along the perimeter wire to identify where the signal is weakening or dropping.
A low voltage reading suggests a break in the wire, a poor connection, or significant interference. This test helps narrow down the source of the problem. If you’re looking for a way to maintain other appliances, you might find this article on azeus-air-purifier-cleaning-and-maintenance helpful.
6. Identifying and Mitigating Interference
External electrical sources can sometimes interfere with the loop signal. Common sources of interference include:
- Power Lines: High-voltage power lines running near your property.
- Electrical Equipment: Transformers, inverters, and other electrical devices.
- Radio Transmitters: Strong radio transmitters can also cause interference.
To mitigate interference:
- Relocate the Base Station: If possible, move the base station away from potential sources of interference.
- Shield the Wire: Consider shielding the perimeter wire with a grounded metal conduit in areas where interference is suspected.
- Use a Filter: Some Husqvarna Automower models offer a filter to reduce interference.
Identifying the source of interference can be tricky, but it’s worth investigating if other troubleshooting steps haven’t resolved the issue.
FAQ: Husqvarna Automower Loop Signal Issues
Q: What does a flashing red light on my Husqvarna Automower mean? A: A flashing red light often indicates a problem with the loop signal, but it can also signify other issues like a blocked mower or a problem with the battery. Consult your owner’s manual for specific error codes.
Q: Can rain affect the loop signal? A: While the system is designed to be weatherproof, heavy rain can sometimes temporarily weaken the signal, especially if there are corroded connections.
Q: How often should I check the perimeter wire? A: It’s a good idea to visually inspect the perimeter wire at least twice a year, and after any landscaping work.
Q: What if I can’t find the break in the wire? A: A professional Husqvarna Automower technician can use specialized equipment to locate hidden breaks in the wire.
Conclusion
Fixing a “No Loop Signal” error on your Husqvarna Automower doesn’t have to be daunting. By systematically checking the connections, inspecting the wire, ensuring proper grounding, and testing the signal strength, you can often resolve the issue yourself. Remember, a strong loop signal is essential for your mower to operate safely and efficiently. Don’t let a weak signal keep you from enjoying a perfectly manicured lawn! If you’ve tried these steps and are still experiencing problems, contact a qualified Husqvarna Automower service technician for assistance.